Welcome to our blog center
You can find tips, basics, guide and more information about manufacturing processes and materials that we have learned from practice here.
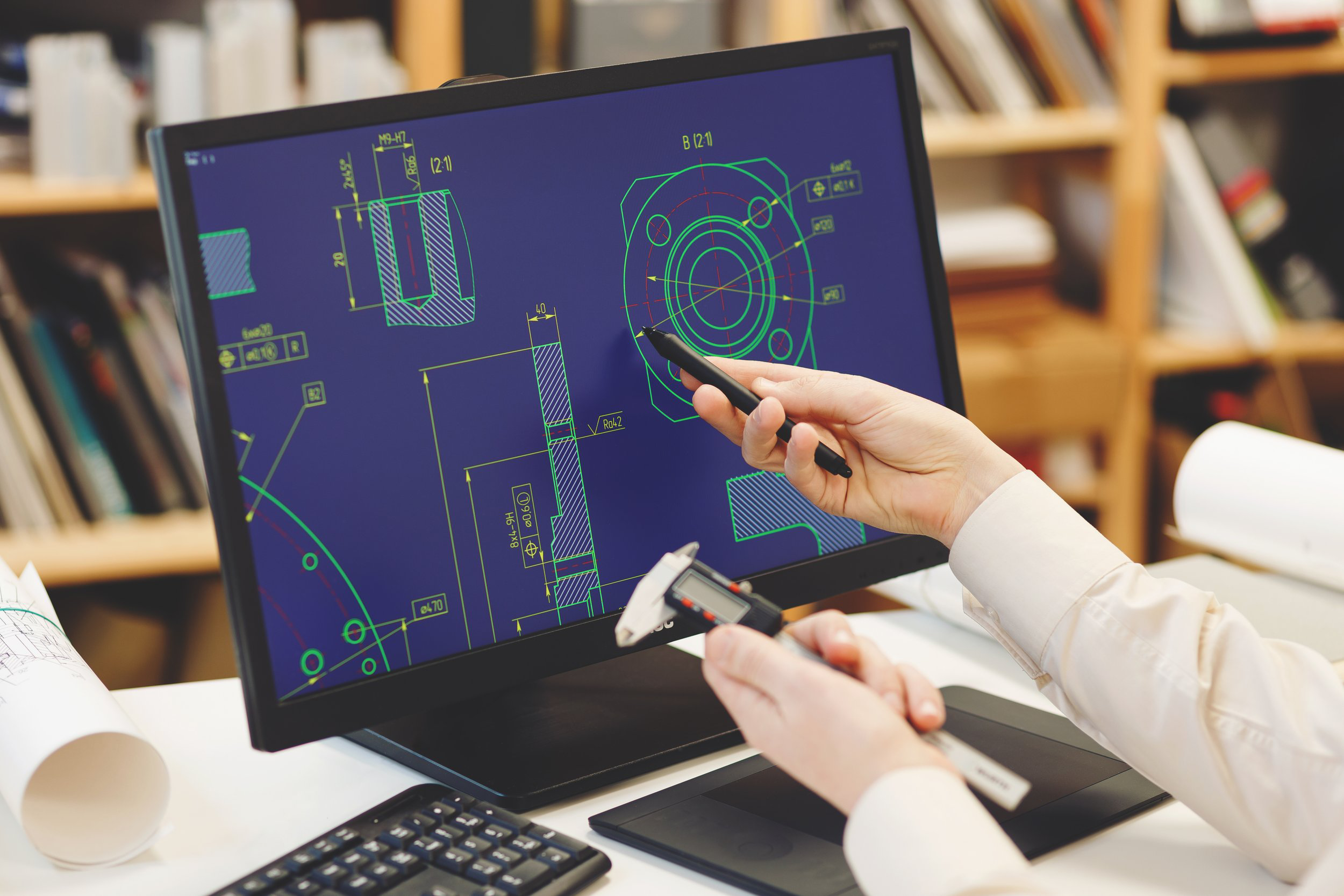
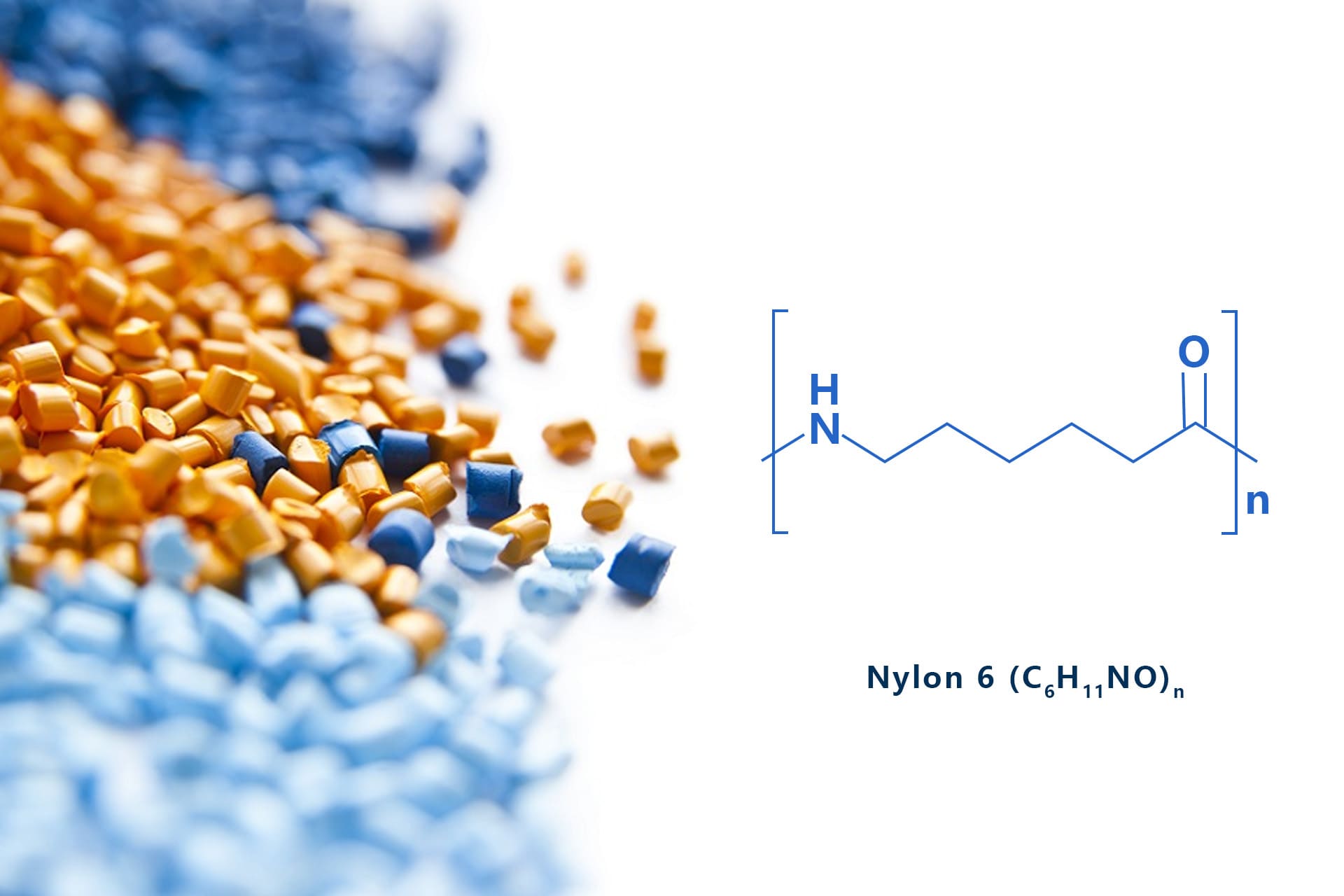
Common Materials in Non-standard Custom Manufaturing
In this article, we have listed 20 types of common materials in non-standard part custom manufacturing.
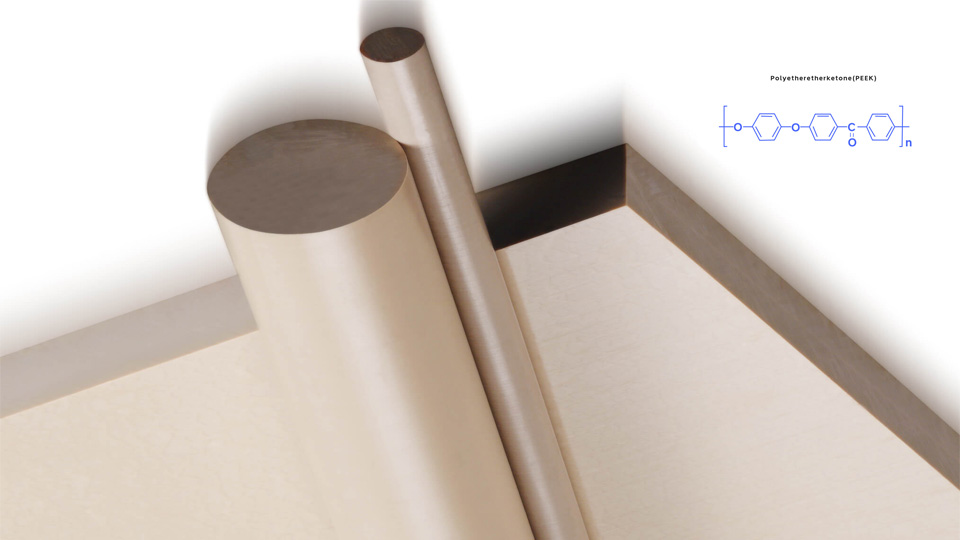
Comprehensive Guide to Properties of PEEK
Polyetheretherketone (PEEK), developed by Imperial Chemical Industries (ICI) in 1978, is a semi-crystalline, linear aromatic polymer composed of alternating ether bonds, aromatic rings, and carbonyl
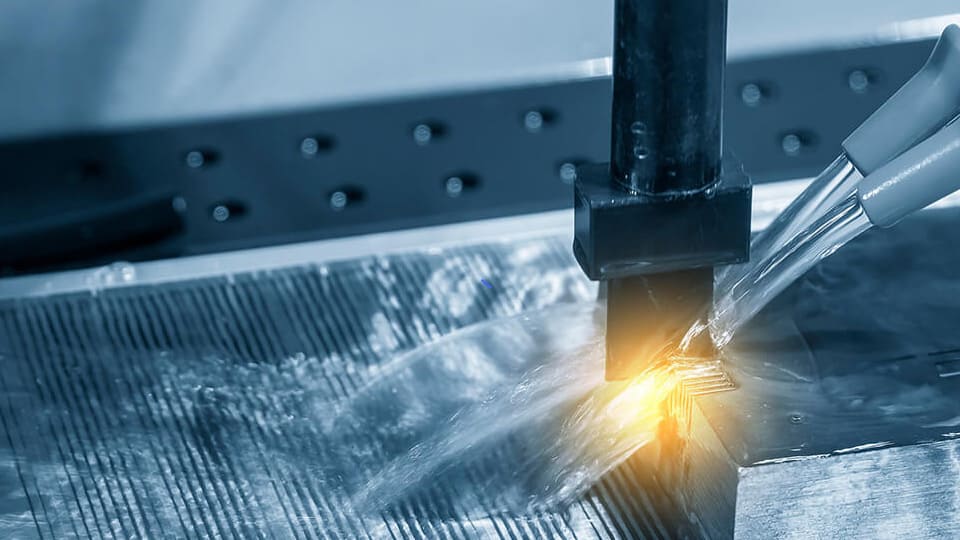
What is Electrical Discharge Machining (EDM)?
EDM uses electrical corrosion from pulsed discharges between a tool electrode and a workpiece electrode to process materials.
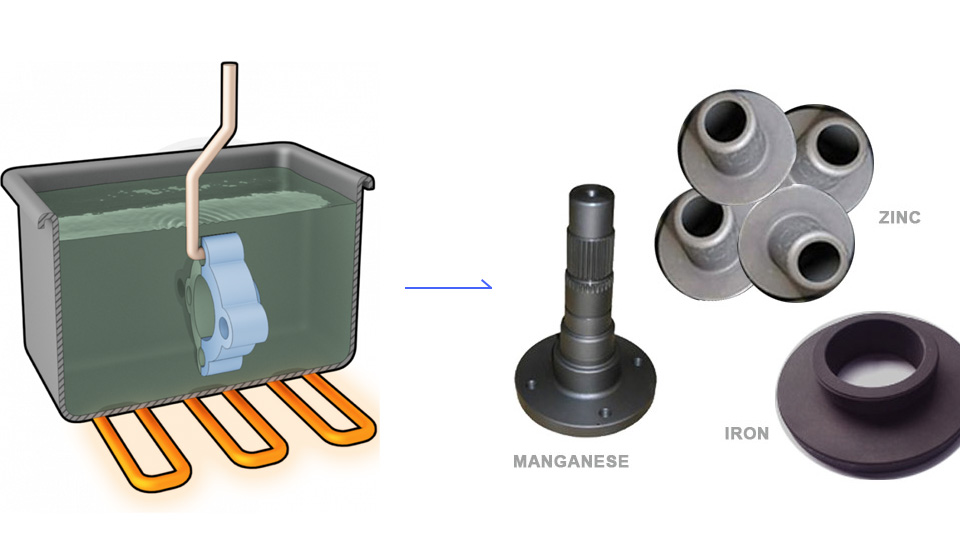
Surface Finish: What is Phosphating Coating?
Phosphating is a process that forms a phosphate conversion coating on a metal surface through chemical and electrochemical reactions.
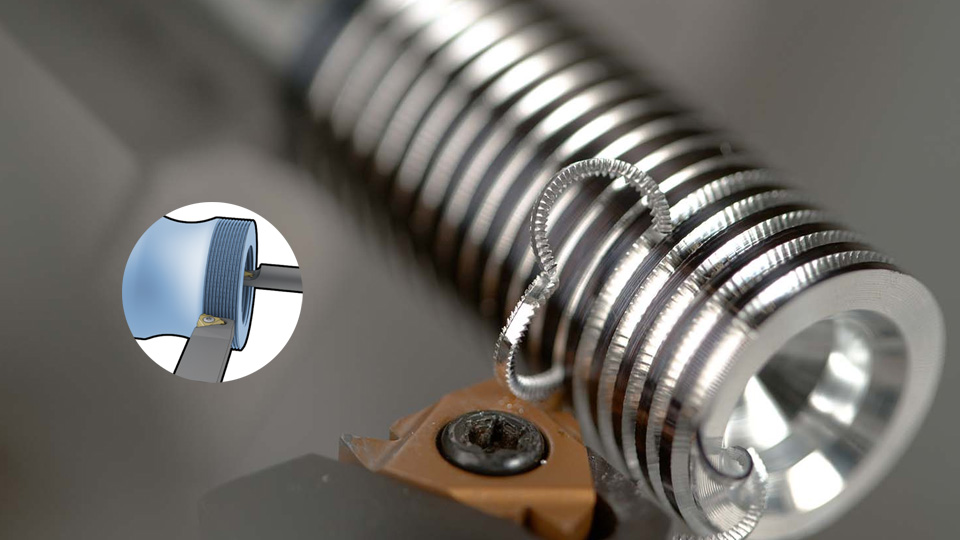
10 Machining Processes to Make Threads in Metals
For connecting threads, processing methods include tapping, turning, rolling, and rubbing. For transmission threads, grinding, or cyclone milling.
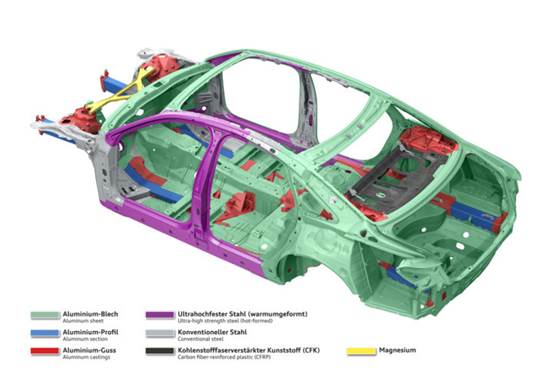
Aluminum Alloys in Automotive Applications
With technological advancements and growing market demand, aluminum usage in small to mid-sized vehicles has increased.
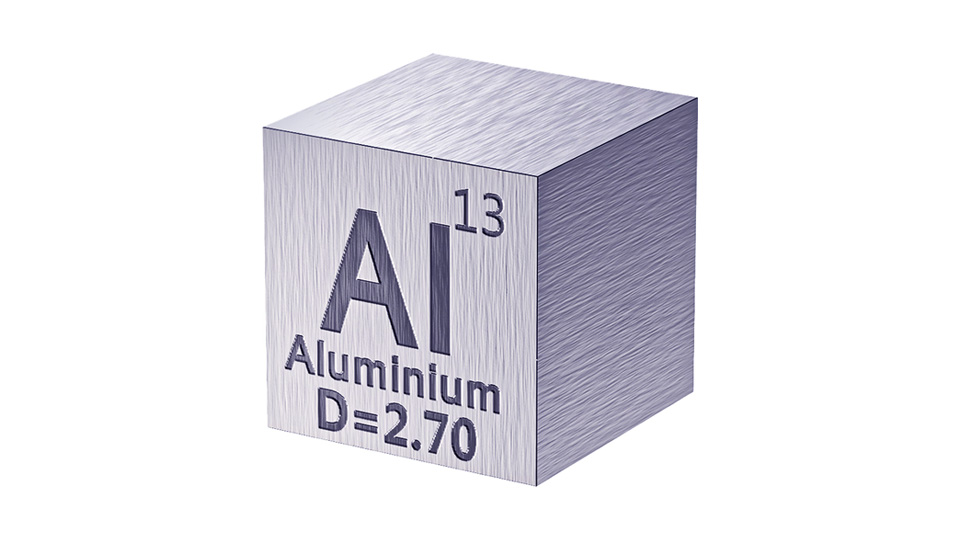
What is the Density of Aluminum?
Aluminum is a soft, lightweight metal. The density of aluminum alloy depends on its alloying elements.
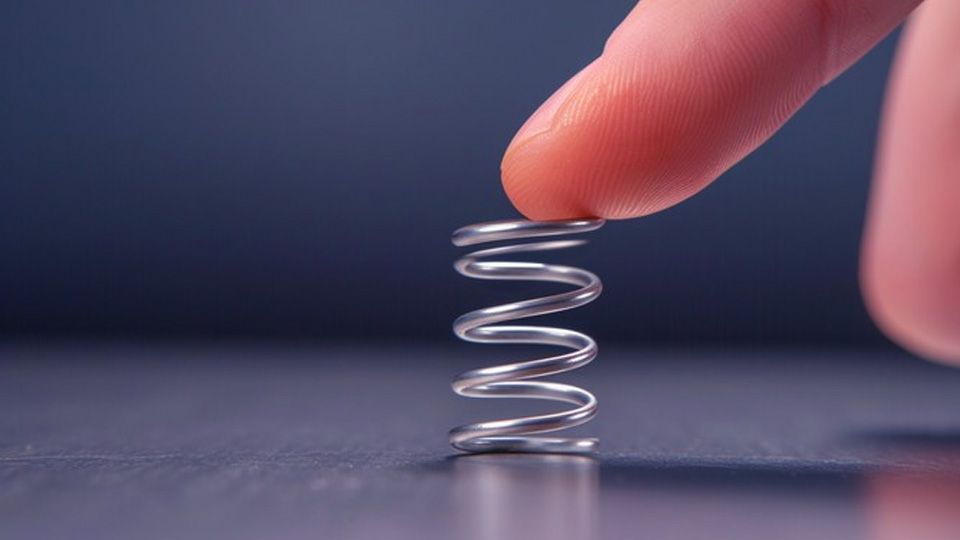
9 Mechanical Properties of Material and How to Measure Them
This article will introduce you to 9 basic mechanical properties of materials: strength, plasticity, hardness, toughness, fatigue, elasticity, stiffness, wear resistance, and corrosion resistance.
SIGN UP FOR US!
Enter your email address to subscribe to our newsletter!
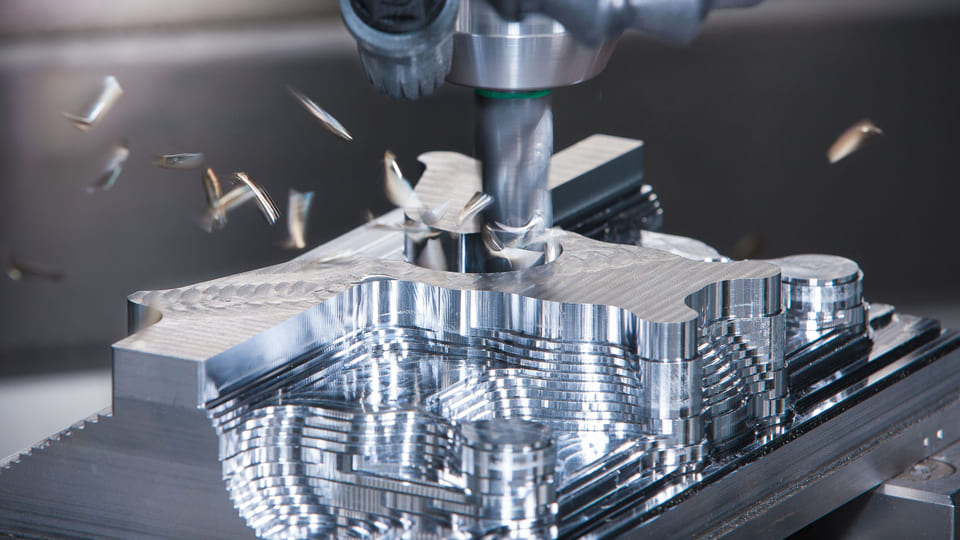
On-demand Manufacturing Services
1 to 1000+ pcs metal or plastic parts, global delivery as fast as 7 days.