Aluminum alloys like 6061 and 7075 are essential materials for modern machines. 6061 has easy bending capabilities, high degrees of corrosion resistance, and weldability for general use. 7075 offers nearly twice the strength but is limited to certain uses such as aircraft and race cars due to its reduced corrosion resistance and poor welding characteristics. This article will explain the differences in mechanical performance and applications of the 6061 and 7075 alloys.
Overview of 6061 Aluminum Alloy
6061 aluminum belongs to the 6000 series of aluminum alloys. Its main elements are magnesium and silicon. The typical composition by weight is:
Al | Si | Zn | Mg | Mn | Cr | Cu | Fe | Ti |
Balance | 0.40 – 0.80 % | 0-0.25 % | 0.80 – 1.20 % | 0-0.15 % | 0.04 – 0.35 % | 0.15 – 0.40 % | 0-0.70 % | 0-0.15 % |
This mix gives 6061 aluminum good strength, weldability, and rust resistance. It is widely used in structural components and automotive parts.
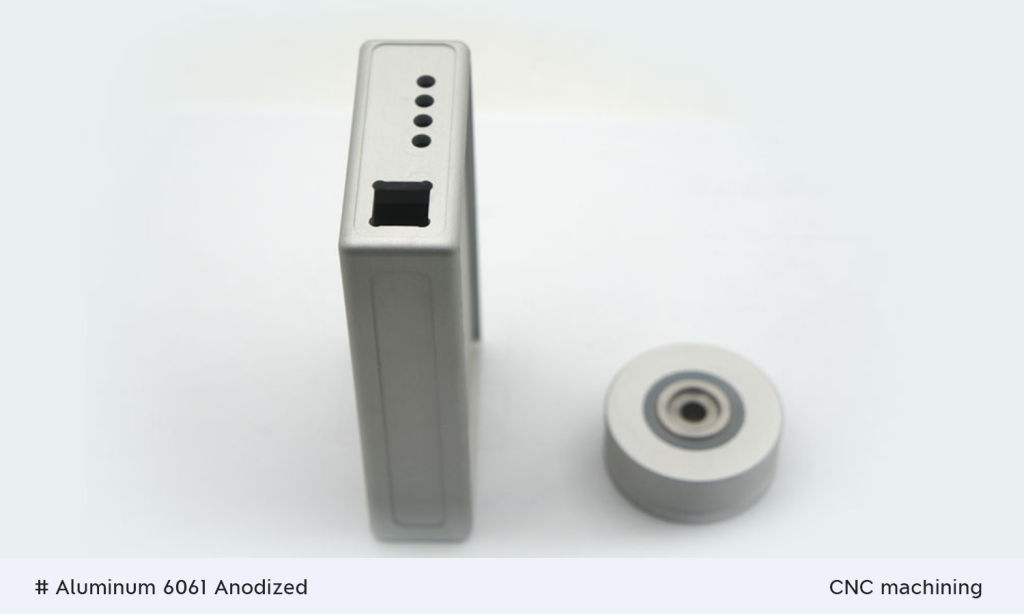
Overview of 7075 Aluminum Alloy
7075 aluminum is part of the 7000 series, with zinc as its main alloying element. Its typical composition by weight is:
Al | Si | Zn | Mg | Mn | Cr | Cu | Fe | Ti | Zr |
Balance | 0 – 0.40 % | 5.6 – 6.10 % | 2.1 – 2.50 % | 0 – 0.30 % | 0.07 – 0.23 % | 1.20 – 1.60 % | 0 – 0.50 % | 0 – 0.2 % | 0 – 0.25 % |
The high zinc content gives 7075 aluminum great strength, reaching up to 560 MPa. It also has good fatigue resistance. But it is less resistant to corrosion than 6061, so protective coatings are often needed.
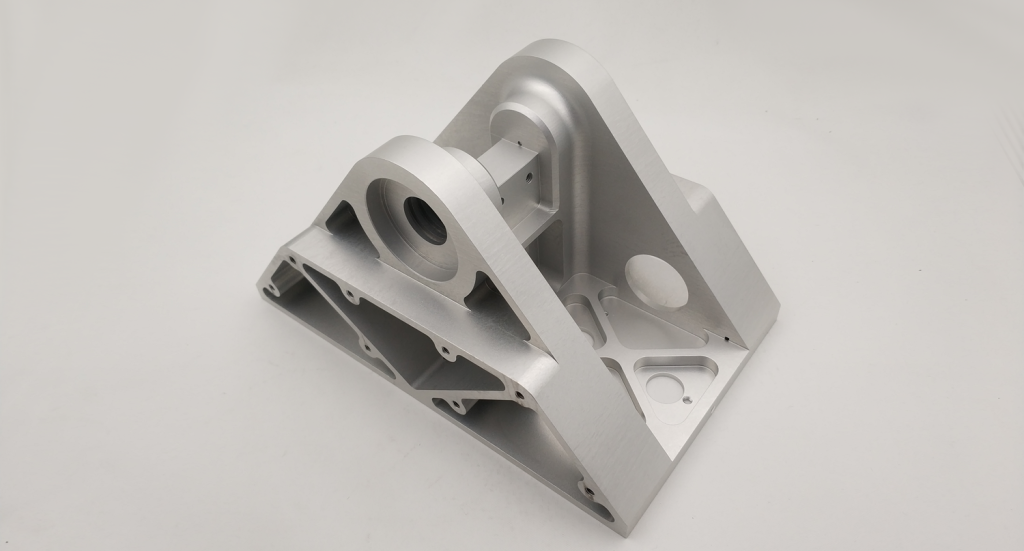
Both alloys are strong and useful but their difference in compositions affect how they perform. 6061 aluminum is best for general use because it welds well and resists corrosion. 7075 aluminum is much stronger, making it ideal for high-stress uses like aerospace parts. Knowing their exact makeup can help manufacturers and engineers choose the right material for their needs.
Alloy Comparison: 6061 vs. 7075
6061 and 7075 aluminum have different mechanical properties, making them useful for different jobs.
Properties | 6061 Aluminum Alloy | 7075 Aluminum Alloy |
Tensile strength | 310 MPa | 560 MPa |
Yield strength | 276 MPa | 480 MPa |
Hardness | 95 HB | 150 HB |
Thermal conductivity | 167 W/m-K | 130 W/m-K |
Melting point | 582 – 652 ℃ | 477-635 ℃ |
Electrical conductivity | 43% IACS | 33% IACS |
Machinability | Good | Fair |
Tensile and Yield Strength
7075 aluminum is much stronger than 6061. In the T6 condition, it has a tensile strength of about 560 MPa, nearly twice that of 6061, which reaches around 310 MPa. Its yield strength is also higher, at about 480 MPa, while 6061 T6 is about 276 MPa. This property makes 7075 a great choice for high-stress applications like aircraft parts and military equipment.
Hardness and Ductility
7075 has a Brinell hardness of 150 HB, meaning it resists dents and wears well. This makes it great for a hard long-lasting application. 6061, on the other hand, is more flexible and can bend without breaking and thus easier to shape and work with.
Shear Strength
The shear strength of 7075 is about 1.5 times that of 6061, this makes 7075 better than the latter in structures that face shear forces. The strength is especially important in aerospace engineering, where materials must be able to take heavy loads without breaking apart.
Corrosion Resistance
Both alloys resist corrosion, but 6061 works better when outside. Its natural oxide layer protects it from the attacks of the weather. 7075 contains more copper, which makes it less resistant to moisture and corrosion.
Density
6061 aluminum averages around 2.70 g/cm³, 7075 aluminum is a bit denser at 2.81 g/cm³. Although is heavier, 7075’s extra density brings it higher strength, making it more suitable for high-stress applications.
Thermal Conductivity
6061 has a thermal conductivity of about 167 W/m·K, meaning it transfers heat well. The heat transfer capability makes it useful for things like heat exchangers. 7075 aluminum has a lower thermal conductivity of around 130 W/m·K, it should be considered carefully in applications where temperature control is significant.
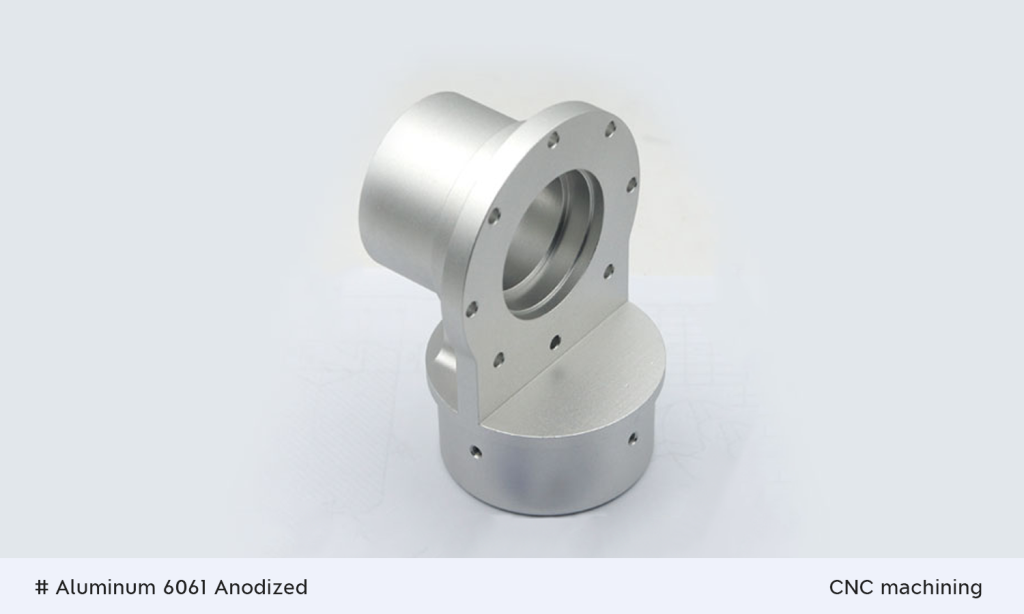
Melting Point
6061 melts between 582 and 652°C (1080–1205°F)and is easy to heat-treat and weld to improve its strength. 7075 aluminum melts at a lower range of 477 to 635°C (890–1175°F), which affects how it is processed.
Electrical Conductivity
6061 aluminum has about 43% IACS conductivity, while 7075 has a lower rating of 33% IACS. This makes 6061 the better choice for applications that need good electrical performance.
Corrosion Resistance
Both alloys resist corrosion due to the protective oxide layer formed on the surface in the air. However, their composition affects how well they hold up. 6061 has more copper, which can lead to corrosion in some conditions. 7075, with its different alloy mix, usually resists corrosion better.
Anodizing
Anodizing coats metal with a tough, decorative layer using electric current in a chemical bath. Aluminum alloys like 6061 (6XXX series) take well to this. The clear coating shields the metal underneath. 7075 alloy also works. It forms the same clear shield but watch zinc levels—much zinc can turn the coating brown.
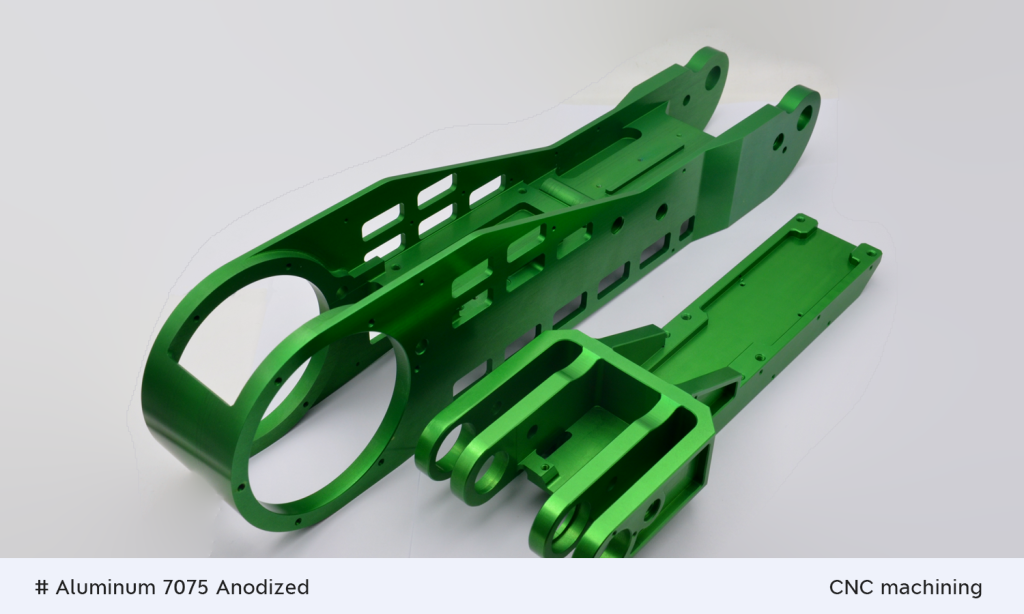
Process for These Alloys
CNC Machining
CNC machining of aluminum, especially alloys like 6061 and 7075, includes several key processes:
CNC Milling: It uses rotating cutting tools to remove aluminum material, creating detailed shapes and features.
CNC Turning: A cutting tool stays in place while the aluminum workpiece rotates, ideal for making cylindrical parts.
CNC Drilling: A rotating drill bit creates precise holes with consistent size and depth.
Welding Process
7075 Aluminum: Hard to weld. Typically requires TIG or laser welding. Preheating (150–200°C) reduces stress, and post-weld aging restores strength.
6061 Aluminum: Easier to weld. Can use TIG, MIG, or laser welding. Usually, no preheating is needed, but thick plates may require moderate heating.
Heat Treatment
Aluminum 7075
- Solution Treatment: Heat to 470-490°C, hold for 1-2 hours, then rapidly quench in water.
- Aging Treatment: Heat to 120-160°C, and hold for 16-24 hours, to enhance strength and hardness.
Aluminum 6061
- Solution Treatment: Heat to 530-550°C, hold for 1-2 hours, then rapidly quench in water.
- Aging Treatment: Heat to 160-180°C, and hold for 8-12 hours, to improve strength and hardness.
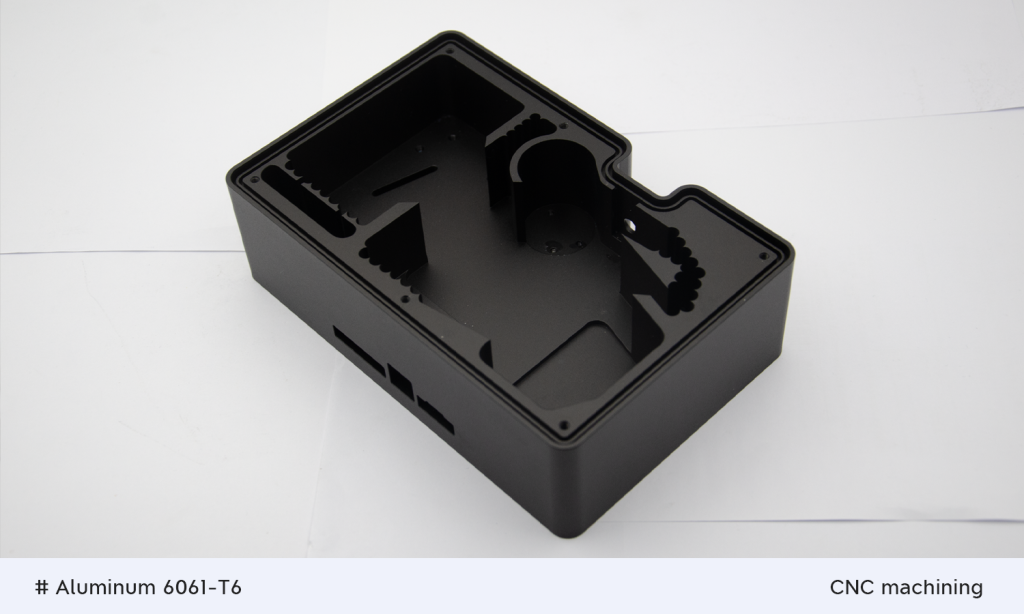
Applications
6061 and 7075 aluminum alloys are widely utilized across various industries due to their distinct properties, which cater to specific application needs.
Aerospace Industry
In the aerospace industry, 6061 aluminum is an ideal material segment for aircraft frameworks, fuselages, and wings since it offers significant resistance to corrosive effects and is enduringly functional relative to its mechanical properties. 7075 aluminum is primarily viewed as an efficient material when composing those high-stressed aircraft components in commercial and military aviation requiring high strength and structural integrity.
Marine Applications
Marine applications include ship hulls, masts, and yacht structures along with utility boats, where 6061 Aluminum is frequently used because of its excellent resistance to saltwater corrosion. 7075 aluminum is occasionally applied in high-performance marine vessels requiring extreme strength, though its lower corrosion resistance limits its widespread application.
Automotive Industry
In the automotive industry, 6061 Aluminum forms light yet tremendously strong materials that raise fuel efficiency and performance used in automobile and bicycle frames, while 7075 Aluminium is used in high-performance automotive components, such as suspension parts and frames, where maximum strength is imperative.
General Manufacturing
General Manufacturing involves Application 6061 aluminum; which is often used for machinery components and molds requiring good weldability and corrosion resistance.7075 aluminum is used in high-stress parts in industrial machinery and tooling, where extreme strength is the primary concern.