In the manufacturing process, one single defect could result in expensive recalls, delayed shipping, or pose safety risks. First Article Inspection (FAI) is one of the most crucial checkpoints that needs to happen before the commencement of mass production, as it verifies that the first unit’s sample complies with each design guideline. By mitigating issues at the onset, FAI helps protect reputations, in addition to saving time and financial resources which is particularly crucial in regulated sectors such as medical devices and aerospace.
One of the most notable benefits of FAI is the confidence it builds among consumers, assuring them that the product meets expectations and is rooted in quality. In this blog, we will detail what the First Article Inspection actually is, its importance from both sides of the aisle, and what the consequences are from skipping or performing hastily. Having a clear understanding of these responsibilities helps ensure effective control of the entire manufacturing process without succumbing to detrimental oversights.
What is a First Article Inspection?
The initial sampling stage of production typically includes a First Article Inspection (FAI). It involves verifying that the initial units produced meet the design and technical specifications. The amount of components checked during FAI is determined by the size of the order. Generally, quantitatively larger orders have a selection of 3 to 5 units chosen through random selection. For smaller runs or prototypes, merely the very first part might be inspected.
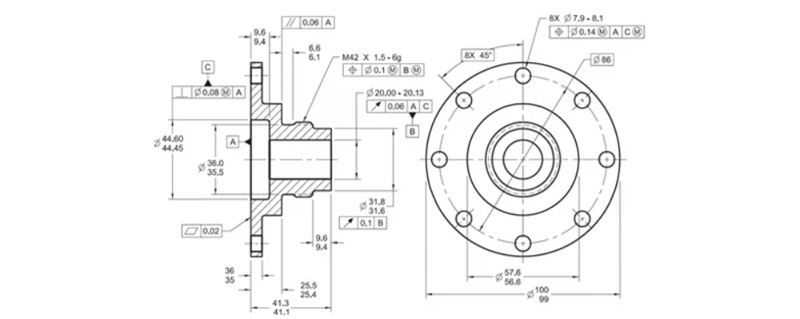
FAI becomes significantly more important when a new part is being created for the first time. It is not as vital for repeat orders where the work has already been proven to function. The First Article Inspection Report (FAIR) details the outcome of the inspection whether the part passed or failed. Production is allowed to proceed if the FAI passes. If it fails, the operation is frozen, corrections are executed, and the part is retested.
Importance of First Article Inspections
First Article Inspections (FAI) are a key part of making sure parts are made right the first time. They help manufacturers catch problems early, avoid costly mistakes, and deliver quality products that meet expectations. Here’s why FAI matters so much:
Confirms the Part Meets Design and Quality Standards
First Piece Inspection Report ensures that the initial part aligns with the design and quality standards. By carrying out measuring and inspecting the initial piece, any disparity or errors will be corrected before triggering full production.
Helps Avoid Expensive Mistakes
Addressing issues early is far more cost-effective than correcting them later in production. During FAI, if there is an issue, it can be fixed immediately instead of waiting until hundreds or thousands of parts are manufactured. This saves time, materials, and finances. Additionally, the risk of excessive rework, scrap, or even recalls is minimized.
Proves Compliance and Traceability
In regulated industries like aerospace, automotive, or medical devices, proof of quality is a must. FAI creates a clear record that the part meets all required standards. This documentation is important for audits, traceability, and showing customers or regulators that everything was done correctly.
Reduces Risk of Delays
Problems that might escalate into more serious concerns are taken care of due to FAI. As a result, the production process can continue seamlessly without having to halt work and can sustain the schedule for phased delivery.
What Goes on a First Article Inspection Report?
As the name suggests, the First Article Inspection Report (FAIR) captures every detail that is critical for the first part of the line including the measurements, materials, test results, and compliance to the specifications. Now let’s look into the basic components of a First Piece Inspection Report:
Part Identification
This is the area that verifies the component being inspected. The part identification section captures the part’s number along with the description, the revision level, and the serial number of the part if there is one. It also incorporates the drawing number relevant to the part and used during production. This captures full traceability and provides easy access for the report and technical documents in version control.
Supplier Information
In this Part, there is identification of the supplier responsible for the part, giving the name and address of the manufacturer or supplier. Provides a contact person, often from the quality or engineering department, who can be contacted in case of any queries or follow-up. This guarantees that the proper mechanisms to answer and establish contact have been put in place.
Product Characteristics
In this area all the dimensions and features of the critical part are listed and assessed. This includes length, diameter, thickness and tolerances which are the allowable limits in variation. It also includes material specifications, in other words, whether the part is made of aluminum 6061 or stainless steel. Required surface finishes are documented here, including coating and texture requirements. This section guarantees all design details are taken into consideration when manufacturing the most complex parts.
Materials and Processes
This section provides details about the raw materials used and how the part was made. It confirms that the materials meet the necessary standards and explains the manufacturing processes involved such as CNC machining, casting, welding, or heat treatment. This helps verify that not just the part, but the way it was made, follows the required procedures.
Inspection Details
This part details the procedures and methods taken in performing the inspection. It discusses tools such as calipers, micrometers, or a CMM (Coordinate Measuring Machine) based on how the part was required to be measured. The date of the inspection is recorded along with the kind of sampling plan implemented, if it was checked 100% or a certain percentage of the sampling. This is done to make certain that this inspection, in particular, is documented properly.
Inspection Results
All actual results from the First piece Inspection Report go here. This includes the measurement values, tests performed, and whether or not every characteristic was per the design specification. Results are documented for any tests that were performed, be they hardness test, leak testing, or fit and function checks. This is where it is clear and evident if the part passes or fails based on the findings from the inspection.
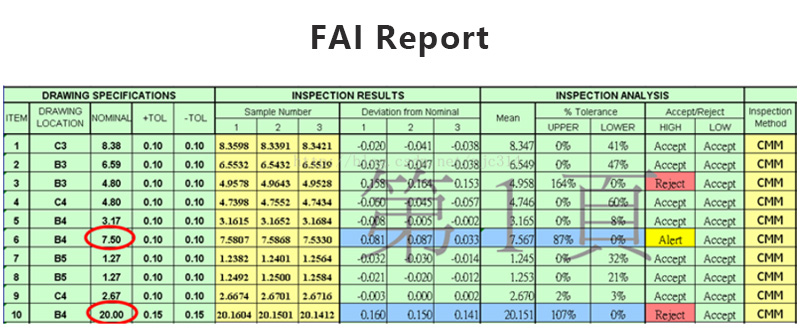
Certifications and Documentation
This is a collection of additional documents pertaining to the inspection. It may include certificates of compliance, proving the part adheres to some industry or customer standards. It may also include some material test reports proving that the materials used indeed meet the right specs. Additional inspection documents such as internal checklists or external test reports may be attached as well. All of these documents support the findings by providing further verification.
Non-Conformance Reports (if applicable)
If the part doesn’t fully meet the design requirements, this section documents what went wrong. It explains the issue such as a measurement being out of tolerance or a defect in the material and describes what action is being taken. That might include reworking the part, scrapping it, or adjusting the process to fix the issue before continuing. This helps prevent the same problem from happening again and shows a commitment to fixing errors properly.
Other Relevant Information
The final section includes approvals, signatures, and any other comments that might be useful. The report is signed off by authorized personnel, often from the quality or engineering team, to officially confirm the results. Any extra notes, observations, or suggestions can be included here to give context or recommendations for future production.
As we can clearly see, the whole procedure of the First Piece Inspection Report goes beyond being just paperwork; rather it is a document that reinforces quality, consistency, and responsibility. Capturing the first part made with all pertinent details through a document, sustaining process, helps avoid problems which in turn helps mitigate delays, enabling full-run production readiness. It is an effective means to bolster supplier and customer relations, one that methodically safeguards the free flow of processes of production.
Tools and Methods Used in First Article Inspection
First Article Inspections, or FAIs, require a range of tools and techniques for them to be done correctly for different functions. Every single tool assists in a given part and to ensure it goes through measurement and evaluation with utmost precision. Let’s go through some of the tools and methods which are most popular.
Coordinate Measuring Machines (CMM)
Also referred to as CMM, coordinate measuring machines help in measuring the complex geometrical shapes and designs with stunning accuracy. Detailed intricate features on complex parts can be easily measured with CMM unlike other manual instruments. CMM uses probes to touch part’s different accessible points and generate a digital map, which is further compared with the original design.
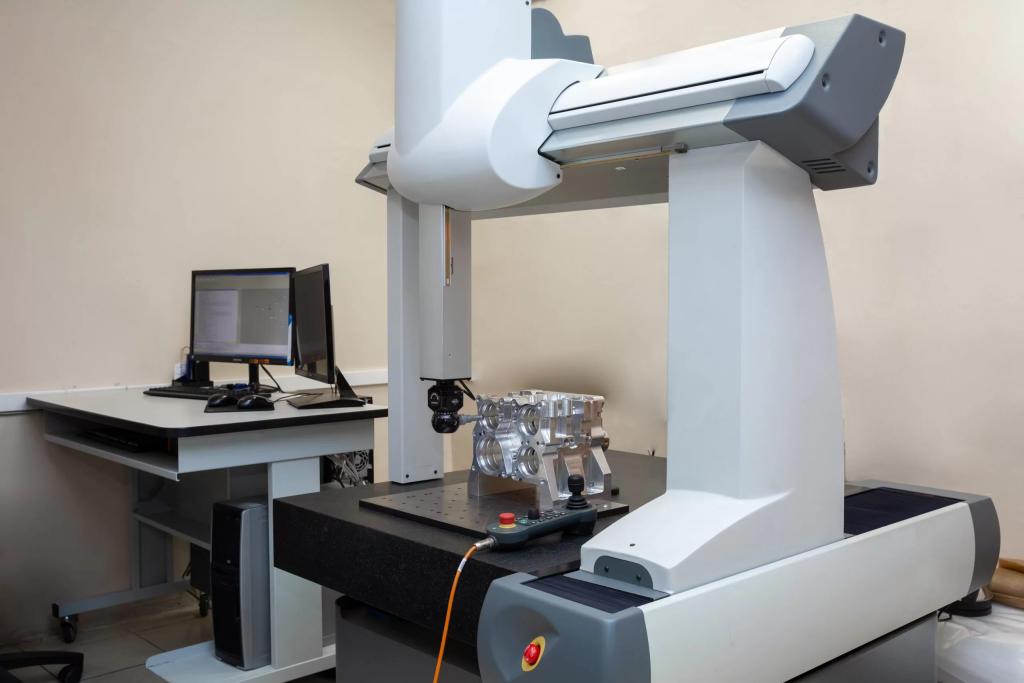
Calipers and Micrometers
Thickness, depth, and diameter are best measured with handheld tools called micrometers and calipers. The instruments do an excellent job measuring small, complex features with strict tolerances. While basic, these tools provide consistent and dependable results when applied correctly.
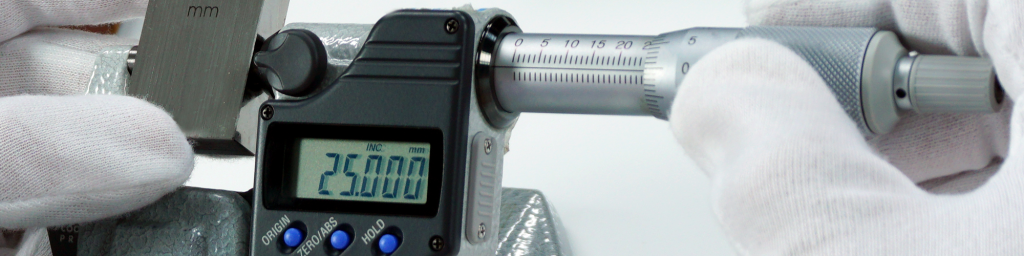
Optical Comparators
As with all comparators, optical comparators employ a projection system to enlarge and show a specific part on a screen. This allows for easy inspection of compliance with standards or measures of set drawings. Optical comparators are best suited for measuring angles, outline profiles, and hole placements in the part.
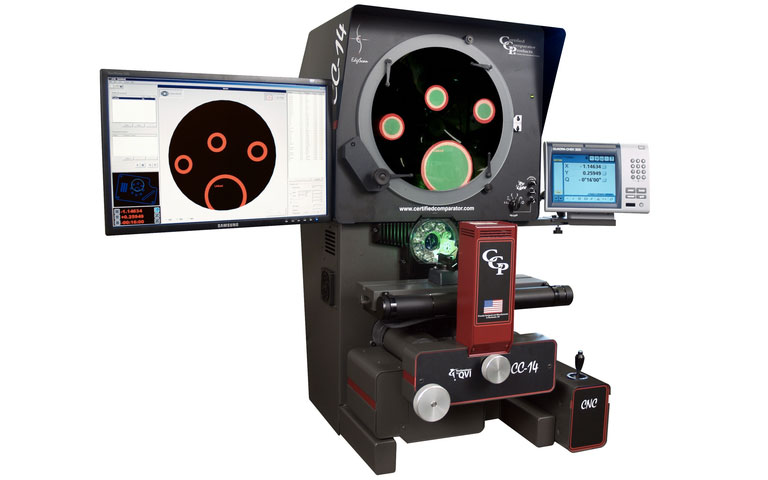
Hardness Testers
These testers are used to measure a certain object’s resistance to indentation. This is very critical for components bound to bear high pressures, wear and tear, and unexpected stress. An inspection during a hardness test helps determine if a part would be useful in the intended service.
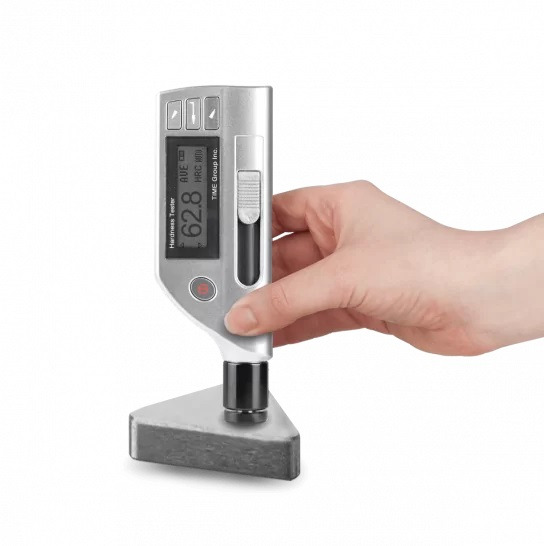
Surface Plates
A surface plate is also known as a base which needs to be flat and stable during manual inspection. It also facilitates as a reference to level out measuring instruments to determine flatness and height. This ensures that all measurements taken are accurate and that the part is aligned according to the design requirements.
Each of these tools plays a key role in making sure the part meets all specifications. These inspectors can determine the quality of the part in regard to its shape and size, as well as its material strength and surface finish.
How to Prepare for a First Article Inspection (FAI)
A successful First Article Inspection begins with meticulous preparation. Proper planning ensures all critical requirements are met before the inspection starts, reducing delays and potential quality issues. The following checklist covers essential preparation steps to verify documentation, equipment, personnel, and samples are ready. By completing these preparatory actions, manufacturers can conduct a thorough and efficient inspection that meets all quality standards.
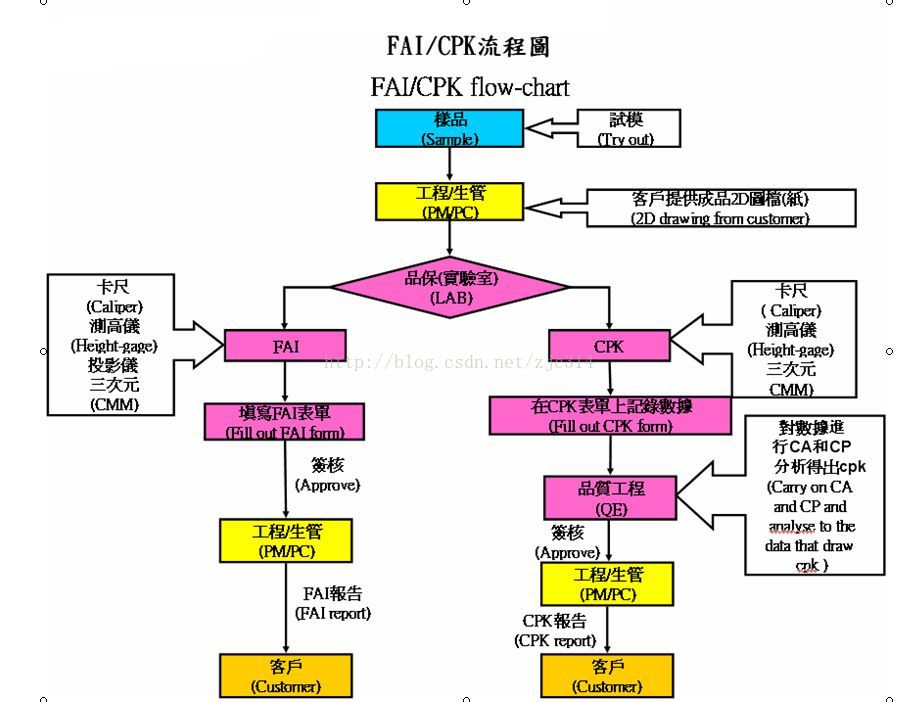
1. Documentation Review
Ensure all engineering drawings are complete and reflect the latest revision. Verify CAD models match current design specifications. Prepare ballooned drawings with all critical features marked for inspection. Gather material certifications (MTRs) and process documentation for reference.
2. Inspection Planning
Define measurement criteria for all critical dimensions to ensure consistency. Establish pass/fail tolerances for each characteristic based on design requirements. Create an inspection sequence and methodology to streamline the process. Identify required inspection equipment and verify its availability.
3. Documentation Verification
Cross-check all part numbers and revisions against engineering documents. Verify material certifications match specified requirements. Confirm process certifications (heat treatment, plating, etc.) are valid.
4. Dimensional Inspection
Measure all critical features using approved methods and tools. Record actual measurements with corresponding tolerance limits. Document any out-of-tolerance conditions immediately.
5. Functional Testing
Perform operational tests if required by design specifications. Validate assembly fits with mating components when applicable. Record all test parameters and results accurately.
6. Surface and Visual Inspection
Examine surface finish against specified requirements. Check for cosmetic defects per acceptance standards. Verify proper deburring and edge conditions.
7. Final Verification
Review all collected data for completeness. Confirm all required characteristics have been inspected. Prepare preliminary disposition recommendation.
8. Reporting and Approval
Complete all required First Piece Inspection Report forms (AS9102 or equivalent). Obtain necessary quality approvals before release. Archive inspection records per document control procedures.
Outputs of a First Article Inspection
The documentation output from a First Article Inspection (FAI) includes the verifications of;
First Article Inspection Report (FAIR)
This is the document that contains all the information that has been gathered after conducting inspections. This includes dimension reports which capture the actual values relative to the drawing specifications, certifications of the materials such as MTRs (Mill Test Reports) which prove the material used, documentation of special processes like plating, heat treatment, and functional tests which prove operational exercises.
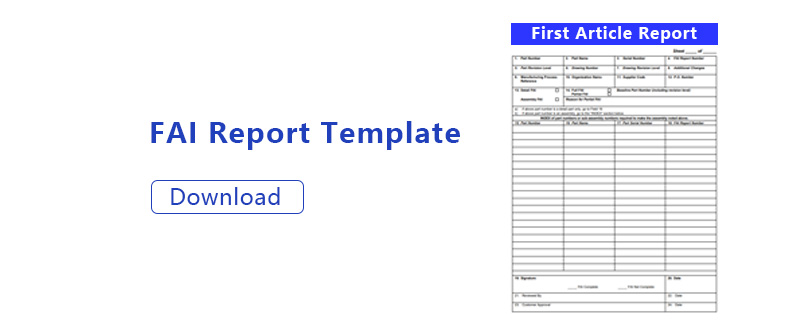
AS9102 Standard Forms (For Aerospace)
The aerospace industry has these three forms under the AS9102 standards. In form 1, Accountability of the part number is provided, which ensures validation of the correct part numbers, drawing revisions, and serial numbers. Form 2 deals with Product Accountability, which captures raw materials, components, and special processes dedicated to them. Characteristic Accountability is documented in form 3 and all features that were measured and served with complaint status are listed.
Ballooned Drawings
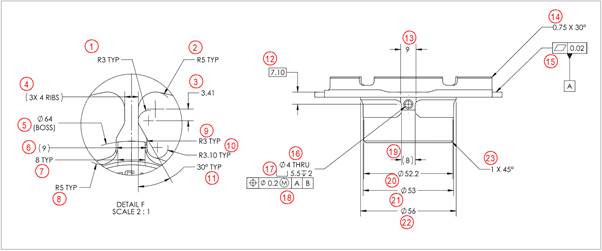
Balloons that identify each inspected element are placed on corresponding engineering drawings. These Ballooned drawings can locate each fundamental dimension including tolerances that are claimed to have been checked and assure the design requirements and inspection outcomes are aligned.
Change Documentation
When design or process changes occur, this documentation captures all modifications. It includes revised engineering drawings reflecting updates, change orders authorizing and describing the changes, and updated material specifications if new materials are introduced.
Approval and Release Documentation
This is the last document set and it verifies that the given part is ready for production. Approval certificates are issued by quality signatories to declare compliance has been met, release notes detail any approved restrictions or conditions of production, and additional verification ensuring that other standards of manufacturing were validated includes Quality Assurance Certifications like ISO or AS9100.
Non-Conformance Reports
During inspection, if discrepancies are found, they get documented through Non-Conformance Reports (NCRs). These documents explain the type of non-conformance, its described impact, as well as what corrective actions have been taken or are planned to resolve the discrepancy.
Supporting Records
Additional documents may include inspection checklists used during the FAI process, calibration certificates for measurement equipment to ensure accuracy, and operator certifications validating that trained personnel performed the inspections.
About SogaWorks
SogaWorks is an all-in-one online platform for custom mechanical parts, connecting over 1,000 top-tier factories to serve startups and major companies. We offer flexible manufacturing solutions for rapid prototyping, small-volume testing, and large-scale production with services like CNC machining, 3D printing, sheet metal fabrication, urethane casting, and injection molding. With our AI-powered quoting engine, SogaWorks can deliver quotes in 5 seconds, match the best capacity, and track every step. This cuts delivery times and boosts product quality.