It is generally known that anodizing is a process of deliberately oxidizing metal surfaces by electrochemical means. Titanium anodizing is a specific application of the anodizing process, whereby the oxidation of titanium metal significantly improves the surface characteristics of production parts, such as enhancing wear resistance and optimizing appearance.
In this paper, we will delve into the methods of implementation of titanium anodizing, the form of the process, as well as the pattern of change in the color of titanium after anodizing and its application in industrial manufacturing.
What is Titanium Anodizing?
Anodizing is an electrochemical process that uses electrical and chemical action to treat the oxide layer of titanium. The titanium part acts as an anode (positive electrode) and is immersed in an aqueous electrolyte solution, such as trisodium phosphate (TSP) or various salts. When energized, the water molecules undergo hydrolysis and break down into hydrogen and oxygen. The electrical potential forces the oxygen to rise to the surface of the titanium and deposit it on a thin layer of titanium oxide. Oxidized metal parts such as titanium act as anodes in electrical circuits. By forming a tough and tightly packed oxide film, these metal surfaces effectively block the penetration of ions, thus preventing or slowing down further corrosion. Overall, titanium anodizing is the electrolytic oxidation of the surface of a titanium (or titanium alloy) part to make the surface properties appropriate for the part’s intended use.
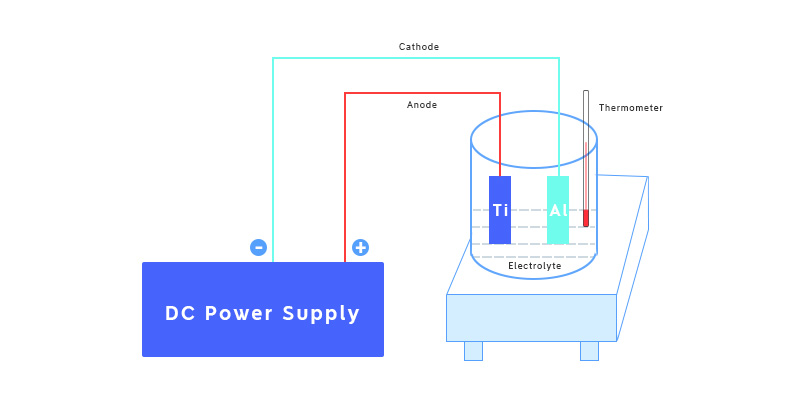
How to Anodize Titanium
To further understand the process of anodizing titanium parts, here are 4 major steps: cleaning, setting up anodizing equipment and tools, electrolysis, control of voltage, current and temperature, and post process.
Step 1: Cleaning
Cleaning is the first step in the process. Before anodizing titanium, it is important to ensure that the surface is free of any contaminants that may affect the adhesion and uniformity of the oxide layer; oil and grease can hinder the anodizing process and may leave imperfections in the anodized titanium that can affect the uniformity and consistency of the color.
Typically, to effectively clean titanium parts, a combination of detergent and water should be used to remove surface contaminants. This step typically involves soaking the titanium part in a cleaning solution and then rinsing with deionized water to remove any residual cleaner. Ensuring that the titanium surface is completely clean will assist in the proper formation of the oxide film during the anodizing process.
Step 2: Setting Up Anodizing Equipment and Tools
Setting up your anodizing equipment is a critical step in ensuring the success of your titanium anodizing process. You will need specific tools and materials, including a power supply that provides the necessary voltage, an anodizing tank with electrolyte, and a cathode, usually made of aluminum foil or stainless steel. The titanium sheet that serves as the anode is connected to the power source, while the cathode is placed in the electrolyte tank.
During setup, it is important to wear rubber gloves to ensure safe operation of the equipment and to avoid contamination. The electrolyte usually consists of sulfuric acid and must be mixed to the correct concentration to facilitate the anodizing process. Precise control of voltage and current is required to form the desired oxide layer on the titanium surface. The anodizing equipment should be checked for proper function to ensure consistent results. Once everything is set up, the electrolysis process can proceed, which is the heart of titanium anodizing.
Step 3: Electrolysis Process
The electrolysis process is an anodic oxidation conversion process that gives titanium parts enhanced surface properties. In this stage, the titanium part is immersed in an electrolyte bath and a direct current is applied through a power supply. The current causes the titanium surface to oxidize, forming an oxide film. The thickness and properties of the oxide film can be controlled by adjusting the voltage and residence time of the titanium in the electrolyte bath.
Step 4: Control of Voltage, Current and Temperature
During the anodizing process, control of voltage, current and temperature is critical to achieving the desired oxide thickness and surface properties. The supply voltage is usually adjusted for the desired oxide film thickness and color, and the current density should be carefully regulated. Typical current densities range from 15-30 amps/sq. ft. to ensure a uniform oxide layer on the titanium surface. Temperature control is also critical; the electrolyte temperature should be maintained between 60 and 75 degrees Fahrenheit to optimize the anodizing reaction and prevent overheating.
Step 5: Post-treatment
Post-treatment is the final step in the titanium anodizing and is critical to sealing and protecting the newly formed oxide layer. Once the anodizing is complete, the titanium part needs to be thoroughly rinsed to remove all electrolyte solutions to prevent any adverse reactions or corrosion. Next is the sealing process, where the anodized titanium part is immersed in a hot deionized water or nickel acetate solution to seal the pores of the oxide layer.
Color Effects of Anodized Titanium
Anodized titanium oxide takes on a range of vibrant colors that are produced by varying the thickness of the titanium oxide layer on its surface. Typically, achievable colors include bronze, purple, blue, light blue, gold, rose, magenta, cyan and green. However, certain colors (e.g., red) cannot be produced by anodizing due to the physical limitations of the interference effect of the oxide layer. Color is directly dependent on the voltage applied during the anodizing process, with the voltage required for different colors ranging from roughly 0 to 100 volts.
A simplified titanium anodizing color chart by voltage is shown below:
Voltage (Volts) | Voltage (Volts) |
0 | Natural (un-anodized) |
0~16 | Bronze |
30-40 | Purple |
40-50 | Blue |
50-60 | Light Blue |
60-70 | Gold |
70-80 | Rose/Magenta |
80-90 | Teal |
90-100 | Green |
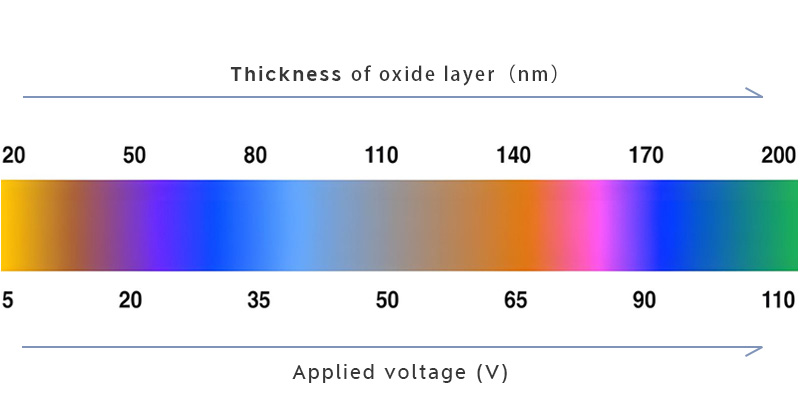
It is important to note that not all colors can be achieved with the titanium anodizing process. Due to the physics of the optical interference phenomenon, red cannot be achieved by conventional anodizing. Currently, the closest colors to red are magenta, rose (reddish-purple) or violet.
Advantages of Titanium Anodizing
1. Enhanced corrosion resistance, proper titanium anodizing can improve the corrosion resistance of titanium and prevent wear and tear
2. aesthetic versatility, through the light interference effect without the need for dyes to obtain bright permanent colors, the color will not fade.
3. Cost-effective and eco-friendly, the process is relatively inexpensive compared to other coatings and avoids the use of harmful chemicals
4. Reduces material friction and wear, anodized surfaces have a higher hardness and reduce material transfer during the friction of mechanical parts
Disadvantages of Titanium Anodizing
1. The precise control of process parameters is difficult, titanium degradation oxidation is extremely sensitive to parameters such as voltage, current, temperature and electrolyte composition, so it is necessary to constantly monitor the fluoride concentration and immersion time, in addition to this any change in the parameters such as tank chemistry, solution temperature, ramp time and other factors may produce oxides of slightly different thicknesses. Precise control of these parameters is challenging in practice.
2. Material limitations and shape complexity increase process difficulty, different grades of titanium alloys react differently to anodizing, not all titanium alloys can be effectively anodized, thus limiting design flexibility
3. Limitations in oxide film performance, while titanium anodic oxides provide some protection, they are limited in thickness and may not provide sufficient protection for high wear applications, and titanium anodizing in oxidant-free environments (e.g., methanol) may not completely prevent corrosion and may even lead to stress corrosion cracking in high titanium alloys.
Titanium Anodizing Applications
Titanium and its alloys have become core materials in the aerospace field due to their light weight, high strength-to-weight ratio and high temperature resistance. However, its susceptibility to corrosion, high oxygen reactivity and surface adsorption problems have restricted wider application. Anodizing can effectively improve the wear resistance, corrosion resistance and optical stability of titanium materials, giving them a unique advantage in precision areas such as space equipment.
Titanium alloys strengthened by anodizing excel in extreme environments and have been expanded into demanding applications such as medical implants, chemical equipment, food processing systems and marine engineering. The technology also enables precise coloration of the material’s surface, which is used in a wide range of applications such as tool size marking, jewelry design, and the surface treatment of high-end consumer products such as bicycles and golf clubs, combining both functionality and aesthetics. The details are as follows.
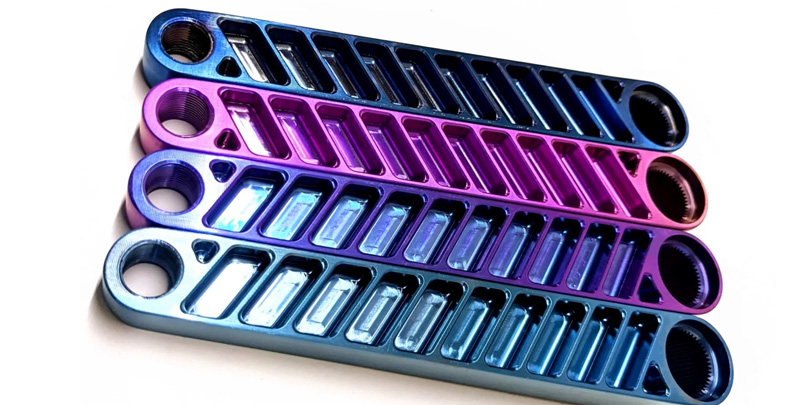
- Aerospace: For corrosion-resistant parts such as fasteners and structural components, weight reduction and durability are critical.
- Medical: Implants (e.g., dental screws, joint prostheses) benefit from biocompatibility and osseointegration properties.
- Mechanical parts: Valves, pumps and mechanical parts utilize reduced friction and wear resistance.
- Decorative: Jewelry, watches and architectural elements utilize vibrant, fade-resistant colors.
- Electronics: Electrically passive surfaces are ideally suited for insulating components in sensitive equipment.
Conclusion
Titanium Anode Oxygen transforms titanium from a cold industrial material into a work of art through controlled voltages and processes. Whether it’s creating sparkling jewelry or enhancing the performance of aerospace components, the possibilities are endless. Try titanium anodizing today and find the perfect balance between function and aesthetics in your designs!
About SogaWorks
SogaWorks is an all-in-one online platform for custom mechanical parts, connecting over 1,000 top-tier factories to serve startups and major companies. We offer flexible manufacturing solutions for rapid prototyping, small-volume testing, and large-scale production with services like CNC machining, 3D printing, sheet metal fabrication, urethane casting, and injection molding. With our AI-powered quoting engine, SogaWorks can deliver quotes in 5 seconds, match the best capacity, and track every step. This cuts delivery times and boosts product quality.