Stainless steel passivation is a surface treatment that enhances the corrosion resistance of stainless steel. It involves forming a dense, stable oxide protective layer on the stainless steel surface through electrochemical methods. This layer prevents direct contact between the stainless steel base metal and external corrosive agents like oxygen, moisture, or other substances, thereby improving the material’s corrosion resistance.
Principle of Acid Stainless Steel Passivation
The corrosion resistance of stainless steel primarily stems from adding more than 10.5% chromium (Cr), for example, 16%–18% in 316L stainless steel. Chromium readily oxidizes, quickly forming a dense Cr₂O₃ oxide film on the steel surface. This film significantly enhances the steel’s electrode potential and corrosion resistance in oxidizing environments. The corrosion resistance of stainless steel relies on this extremely thin (about 1 nm) and dense passivation film, which acts as the primary barrier, isolating the base metal from corrosive media. If the passivation film is incomplete or damaged, stainless steel can still corrode.
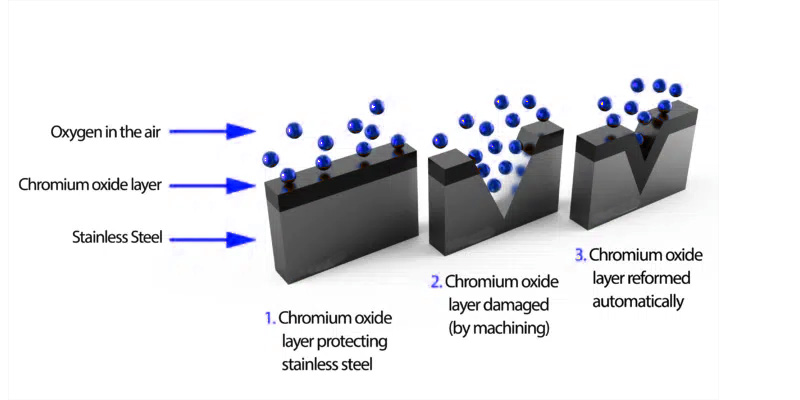
When stainless steel is exposed to air, it forms an oxide film, but this film’s protective properties are inadequate. Acid pickling removes an average surface layer of about 10 μm, where the chemical activity of the acid causes defective areas to dissolve faster than other parts of the surface. This process results in a more uniform and balanced surface. More importantly, acid pickling and passivation preferentially dissolve iron and its oxides over chromium and its oxides, eliminating the chromium-depleted layer and enriching the surface with chromium. Under the action of an oxidizing agent, a complete and stable passivation film forms. This chromium-rich passivation film can reach a potential of +1.0V (SCE), close to that of noble metals, significantly enhancing corrosion resistance stability.
Significance of Stainless Steel Passivation
The primary reason for the widespread use of stainless steel is its corrosion resistance, which extends the lifespan of components made from it. However, stainless steel is not immune to rust. All stainless steel materials, unless plated or coated, typically undergo passivation after pretreatment (such as acid pickling to remove black scale, polishing, etc.) for use as finished products or in assemblies. Evidence shows that only through passivation can stainless steel maintain long-term passivation stability, thereby improving its corrosion resistance.
Related Post: Does Stainless Steel Rust? Everything You Need to Know
Methods of Passivation
Depending on the operation, stainless steel acid pickling and passivation can be performed using six methods: immersion, paste, brushing, spraying, circulation, and electrochemical. Among these, immersion, paste, and spraying are particularly suitable for acid pickling and passivation of stainless steel chemical tankers and equipment.
Immersion Method
The immersion method is ideal for stainless steel pipelines, elbows, and small components, offering the best treatment results. The parts are fully submerged in the pickling and passivation solution, allowing complete surface reaction and the formation of a dense, uniform passivation film. This method is suitable for continuous batch operations but requires periodic replenishment of the solution as its concentration decreases. Its drawbacks include limitations due to the shape and capacity of the acid tank, making it unsuitable for large equipment or overly long or wide pipelines. Prolonged disuse may reduce effectiveness due to solution evaporation, and it requires dedicated venues, acid tanks, and heating equipment.
Paste Method
Stainless steel pickling and passivation paste is widely used and available in various commercial products, typically composed of nitric acid, hydrofluoric acid, corrosion inhibitors, and thickeners in specific proportions. It is suitable for on-site applications, such as treating weld seams, weld discoloration, ship deck tops, corner dead zones, escalator backs, and large-area passivation inside liquid tanks.
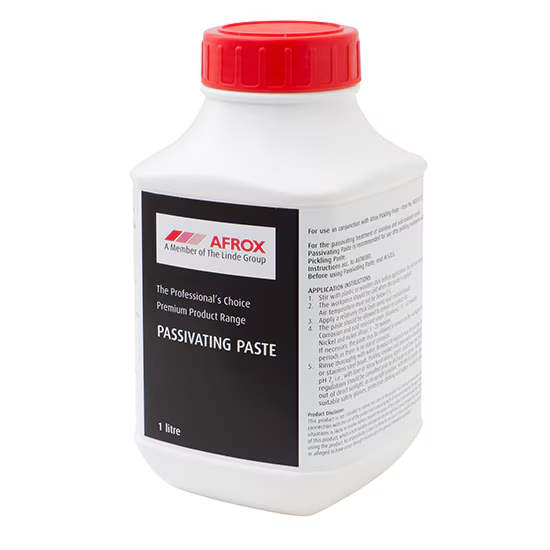
The paste method’s advantages include no need for specialized equipment or venues, no heating requirements, flexible on-site operation, and one-step pickling and passivation. The paste has a long shelf life, with each application using fresh paste, and the reaction stops after passivation, avoiding over-corrosion. It is less affected by subsequent rinsing time, and weak areas like welds can be further strengthened. However, the worker’s operating environment is poor, labor intensity is high, costs are higher, and the treatment effect on the inner walls of stainless steel pipelines is less effective, requiring a combination with other methods.
Spraying Method
The spraying method is suitable for fixed, enclosed environments with single products or equipment with simple internal structures, such as spray pickling processes on sheet production lines. Its advantages include fast, continuous operation, simple operation, minimal impact on workers, and high solution utilization, as the pipeline can be re-pickled during the transfer process.
Considerations of Passivation
Pretreatment for Acid Pickling and Passivation: If grease or other contaminants are present on the stainless steel surface, they can affect the quality of pickling and passivation. Generally, alkaline detergents or cleaning solutions should be used to clean the inner walls of the tank first.
Control of Chloride Ion Concentration in Pickling Solution/Paste and Cleaning Water: Excessive chloride ions can damage the stainless steel passivation film. Some pickling solutions or pastes use chloride-containing corrosive media like hydrochloric acid or perchloric acid as primary or auxiliary agents to remove surface oxide layers, which is detrimental to corrosion prevention. Standards, such as CB/T3595-94 for stainless steel pickling and passivation paste, require chloride ion content to be controlled between 25 ppm and 100 ppm. Cleaning water should also have chloride ion levels below 25 ppm, which can be achieved by adding sodium nitrate as a chloride ion corrosion inhibitor to tap water during construction.
Waste Liquid Neutralization and Environmental Discharge: Acid pickling and passivation waste liquid must meet national environmental discharge standards. For example, fluoride-containing waste can be treated with lime milk or calcium chloride, while chromium-containing waste can be reduced with ferrous sulfate.
Quality Inspection of Passivation
The quality of stainless steel pickling and passivation can be inspected according to standards like CB/T3595-94 for stainless steel pickling and passivation paste or ISO 15730 for surface passivation film inspection after electrolytic polishing, grinding, and pickling passivation. Common inspection methods include:
Visual Inspection: The pickled and passivated stainless steel surface should be uniformly silver-white, smooth, and aesthetically pleasing, with no visible corrosion marks. Weld seams and heat-affected zones should have no oxidation discoloration, and there should be no uneven color spots.
Residual Liquid Inspection: Use phenolphthalein test paper to check the rinsing degree of residual liquid on the stainless steel surface; a neutral pH value indicates a pass.
Blue Dot Test: The blue dot test is based on the principle that incomplete passivation films or iron ion contamination will result in free iron ions, which react with potassium ferrocyanide solution to form a blue precipitate according to the reaction:
K⁺ + Fe²⁺ + [Fe(CN)₆]³⁻ → KFe[Fe(CN)₆]↓
Test Method: Dissolve 10g of potassium ferrocyanide in 50ml of distilled water, add 30ml of concentrated nitric acid, and dilute to 1000ml with distilled water in a volumetric flask to prepare the blue dot test solution, which has a one-week shelf life. Drop the test solution onto the test paper attached to the stainless steel surface; if blue dots appear on the test paper after 30 seconds, the surface is deemed unqualified.
About SogaWorks
SogaWorks is an all-in-one online platform for custom mechanical parts, connecting over 1,000 top-tier factories to serve startups and major companies. We offer flexible manufacturing solutions for rapid prototyping, small-volume testing, and large-scale production with services like CNC machining, 3D printing, sheet metal fabrication, urethane casting, and injection molding. With our AI-powered quoting engine, SogaWorks can deliver quotes in 5 seconds, match the best capacity, and track every step. This cuts delivery times and boosts product quality.