Plastics are everywhere in manufacturing and daily life, they play a huge role in the quality and safety of the final products we use. Among their many properties, the melt point is a key factor for plastics, shaping everything from how they’re processed to where they’re used and how they’re recycled. This article dives into a study of the melting points of common plastics, offering practical insights to guide the processing and application of plastic parts effectively.
What is Melt Point of Plastics?
Melt point of a plastic refers to the specific temperature at which a thermoplastic polymer transitions from a solid to a liquid (molten) state, characterized by the disruption of its crystalline structure (if present) under standard atmospheric pressure. This definition applies primarily to semi-crystalline thermoplastics, as amorphous plastics lack a distinct melting point and instead exhibit a glass transition temperature (Tg), where they soften gradually into a viscous state.
Semi-crystalline plastics have both crystalline and amorphous regions. Their melting point reflects the melting of crystalline domains, quantified as the temperature at which the crystalline fraction transitions to a melt.
Amorphous plastics lack a true melting point due to the absence of crystalline structures. Instead, they undergo a glass transition (Tg), where the polymer chains gain sufficient mobility to shift from a rigid, glassy state to a rubbery or viscous state. For example, polystyrene has a Tg of ~100°C, but no distinct melting point.
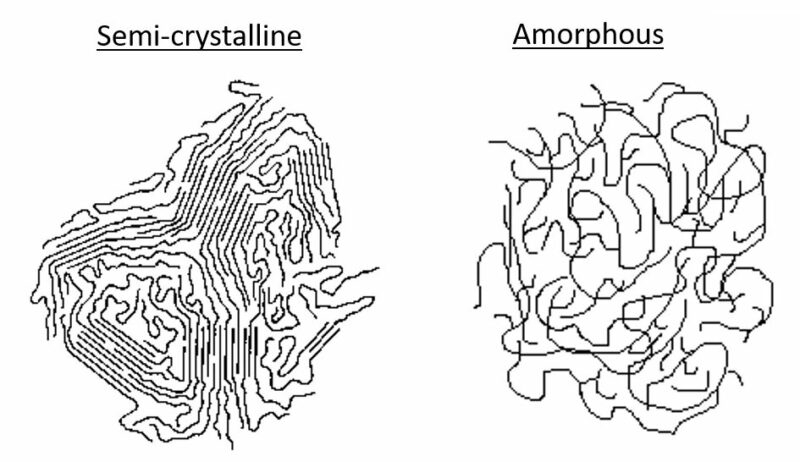
Factors Influencing Melt Point
Molecular Structure: The melting point is governed by the polymer’s chemical composition, chain length, and degree of crystallinity. For instance, stronger intermolecular forces (e.g., in polyamides with hydrogen bonding) result in higher melting points (e.g., nylon, ~220-260°C).
Additives and Blends: Plasticizers, fillers, or copolymers can alter the melting point by disrupting crystallinity or modifying chain interactions. For example, adding plasticizers to PVC may lower its effective processing temperature.
Degree of Crystallinity: Higher crystallinity increases the melting point and sharpness of the transition, as more energy is required to disrupt ordered regions.
Molecular Weight: Higher molecular weight polymers may exhibit slightly elevated melting points due to increased chain entanglement, though this effect is secondary compared to chemical structure.
Why You Need to Know the Melting Point of Plastics?
Knowing the melting point of plastics is super important in fields like manufacturing, product design, and material science. Here’s why it matters in a clear, everyday way:
Getting manufacturing right
The melting point is the key to shaping plastics through processes like injection molding or extrusion. For example, polypropylene (melts around 130-170°C) needs just the right heat to flow smoothly without burning or breaking down. You get better products, less waste, and lower energy costs after knowing this fact. After all, no one wants a gooey mess or a huge power bill!
Choosing the perfect plastic
Different plastics handle heat differently. Teflon (melts around 327°C) is awesome for high-heat jobs like non-stick pans, while low-density polyethylene (melts around 115-135°C) is great for lightweight packaging but would melt in hot conditions. Knowing the melting point helps pick a plastic that won’t flop when things get toasty.
Keep It Safe and Compliant
In food or medical industries, the melting point is a safety must. Picture a plastic food container that needs to survive a dishwasher or microwave without melting or leaking harmful stuff. Understanding melting points ensures products meet tough safety rules, like FDA or EU standards, so your food stays safe.
Making recycling easier
Recycling plastics is like solving a puzzle, and the melting point is a big clue. Plastics like PVC melt at different temperatures, and mixing them can ruin the process or break equipment. Knowing the melting point helps sort and recycle plastics properly, which is great for the environment.

Building products that last
If you’re designing something like car parts near a hot engine, you need a plastic that can take the heat, like nylon (melting around 220-260°C). Choose one with a low melting point, and you’ll end up with warped or melted parts. The melting temp. helps create stuff that stays strong, no matter what.
Ensure product quality
The melting point is like a plastic’s ID card—it shows if the material is pure or if something’s wrong, like contamination. Scientists use tools like DSC to test this, ensuring the plastic is exactly what you need. Nobody wants a bad batch messing up their project.
Melting Point of Different Plastic Materials
These semi-crystalline plastics have both crystalline and amorphous regions, giving them a defined melting point where the crystalline structure breaks down into a molten state. They’re typically strong, heat-resistant.
Melt Point for Common Plastics
Materials | Tm (Metric) | Tm (English) |
HDPE | 130 – 140 °C | 266 – 284 °F |
LDPE | 110 °C | 230 °F |
PP | 130 – 170 °C | 266 – 340 °F |
PA6 | 235 °C | 455 °F |
PA66 | 262 °C | 504 °F |
POM | 165 °C | 329 °F |
PTFE | 327 °C | 620 °F |
These amorphous plastics have a random molecular structure, so they lack a distinct melting point and instead soften gradually at their glass transition temperature (Tg). They’re often transparent, flexible, or impact-resistant but less heat-resistant.
Tg for Common Plastics
Materials | Tg (Metric) | Tg (English) |
PS | 95 °C | 203 °F |
PVC | 110 °C | 230 °F |
ABS | 100 °C | 212 °F |
PC | 145 °C | 293 °F |
PMMA | 90 °C | 194 °F |
PEEK | 140 °C | 284 °F |
About SogaWorks
SogaWorks is an all-in-one online platform for custom mechanical parts, connecting over 1,000 top-tier factories to serve startups and major companies. We offer flexible manufacturing solutions for rapid prototyping, small-volume testing, and large-scale production with services like CNC machining, 3D printing, sheet metal fabrication, urethane casting, and injection molding. With our AI-powered quoting engine, SogaWorks can deliver quotes in 5 seconds, match the best capacity, and track every step. This cuts delivery times and boosts product quality.