4140 steel is a low-alloy steel with great strength, toughness, and wear resistance. It belongs to the AISI—American Iron and Steel Institute—alloy steel series and is quite versatile. It has a broad range of uses across various industries. Here are some of the key properties of 4140 steel, applications, and considerations.
What is 4140 Steel?
4140 is a low-alloy steel with the main alloying elements being carbon, chromium, and molybdenum. That chemical composition will endow 4140 steel with high mechanical properties and some corrosion resistance. The hardness and toughness of 4140 steel can be modified by various heat treatment processes, such as quenching and tempering. It has a good performance for the price and hence finds a very wide field of application among all steels used in industry.

Chemical Composition
The chemical composition of AISI 4140 steel is as follows.
Fe | C | Cr | Mn | Si | Mo | P | S |
Balance | 0.38 – 0.43% | 0.8 – 1.1% | 0.5 – 1% | 0.15 – 0.3% | 0.15 – 0.25% | 0.035% | 0.04% |
These elements combine to achieve excellent overall mechanical performance in the steel. For instance, carbon contributes to hardness and strength; chromium improves corrosion resistance as well as wear properties. Manganese enhances hardenability, while silicon helps in deoxidation, strengthening the structure of the steel.
4140 Steel Equivalents
4140 alloy steel chemical composition has different names in other parts of the world according to regional standards.
USA (ASTM) | China (GB/T) | UK (BS) | Germany (DIN) | Japan (JIS) | France (NF) |
4140 | 42CrMo | 708M40 | 42CrMo4 | SCM440 | 40CD4 |
Heat Treatment of 4140 Steel
Heat treatment is one of the important processes that enhance the mechanical properties of 4140 steel, which is a low-alloy steel with high strength and toughness. Hence, it can be applied to different industrial fields. The basic heat treatment processes usually include Annealing, Normalizing, Tempering, and Quenching, each having a great influence on the microstructure and overall performance of the steel.
Annealing
Annealing is the softening of the steel, making machining and related operations easy.
- Heat your workpiece in the furnace to 1450 – 1600°F.
- Hold for 1 hour (more time for thicknesses above 1 inch).
- Shut off the furnace and let the metal cool within.
Normalizing
Improve mechanical properties.
- Heat your workpiece in the furnace to 1600 – 1700°F.
- Hold at least 30 minutes, more is better.
- Take the metal out of the furnace and let cool in still air.
Quenching
Optimum strength and toughness.
- Heat in your furnace to 1550 -1600°F
- Hold for at least 30 minutes per inch of thickness
- Remove from the furnace and immediately quench the workpiece in mineral oil.
- When the workpiece cools to 150°F, begin tempering.
Tempering
Lessen brittleness and danger of cracking. Lower temperatures will result in increased tensile strength; at higher temperatures the tensile strength will be less. Expect a solid 225 ksi tensile strength (as well as hardness of 50 HRC) at 600°F, dropping to about 130 ksi at 1000°F.
- Heat in your furnace to 400 – 1200°F.
- Hold at temperature for 15 minutes per inch of thickness.
- Remove from the furnace and air cool.
Key Properties of 4140 Steel
The mechanical properties of 4140 Steel are as follows.
Yield strength (MPa) | 415 |
Tensile strength(MPa) | 655 |
Hardness(HB) | 197 |
Elogation(%) | 25.7 |
Machinability | 65% |
Advantages of 4140 Steel
When considering the use of AISI 4140 steel in industrial projects, it is important to weigh its pros and cons to make sure that it meets the specific needs of a project.
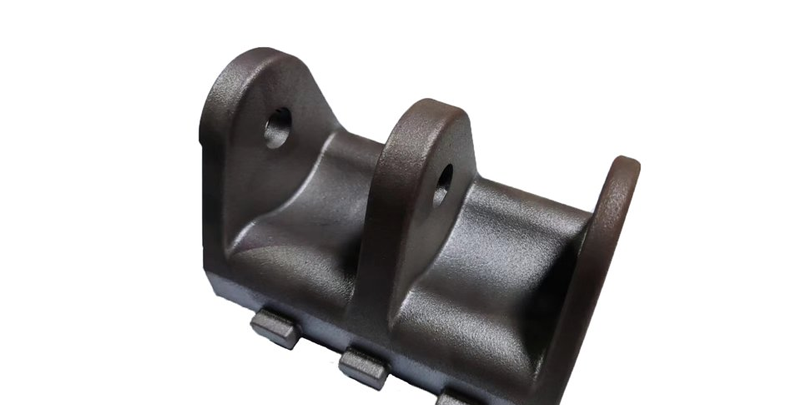
Advantages of 4140 Steel
High Hardness and Strength. The alloy has a nicely balanced combination of hardness and strength, which is especially useful when manufacturing forged parts such as gears, axles, and shafts.
Good Wear Resistance. The composition of 4140 steel, with alloying elements like chromium and molybdenum, considerably enhances its wear resistance. These elements significantly help in increasing the material’s ability to resist abrasion while maintaining optimum performance under high-stress conditions.
High Toughness. Among the major characteristics of 4140 steel is toughness; the hardness of softened 4140 steel is typically 192 HB on the Brinell scale. However, it can achieve a higher level of hardness by heat treatment methods involving quenching and tempering.
Exceptional Fatigue Resistance. 4140 contains a high level of fatigue resistance. The presence of high tensile strength, along with good stress distribution, will reduce the initiation of cracks; therefore, it contributes to a longer life when under cyclic loading conditions.
Disadvantages of 4140 Steel
Poor Weldability. the 4140 steel has a high tendency for weld cracking, so special care, such as pre-heating and post-heat treatment, can be necessary for the welding of this steel.
Medium Machinability. While 4140 steel possesses good malleability, its cutting and machining performance is only medium. It may involve high cutting speeds and perhaps tool wear.
High Hardenability. This means that the cooling rates must be carefully controlled in processing to avoid unwanted heat treatment effects like distortion or cracking.
Steel 4140 vs. Other Alloys
4140 vs. 1045 Steel
4140 alloy steel is often compared to 1045 steel, which falls under the group of medium-carbon steels. While 1045 steel has good machinability and fair tensile strength, it lacks chromium and molybdenum alloying elements found in 4140, which gives rise to low hardenability and poor wear resistance. In direct contrast, due to its makeup, 4140 can outperform in applications requiring improved strength and toughness.
4140 vs. 4130 Steel
4140 steel has a higher steel content compared to 4130 steel. 4140 steel also has more strength and hardenability compared to 4130 steel. On the other hand, 4130 steel has better weldability than 4140 but with less wear resistance.
4140 vs. 4150 Steel
The comparison of 4140 with 4150 steel shows some significant differences in carbon content. While 4140 contains 0.38% to 0.43% carbon, 4150 steel contains more carbon, ranging from 0.48% to 0.53%, thereby giving more strength and hardness to 4150. This makes it more suitable where high wear resistance is required, especially in firearm barrels and high-strength bolts. Its increased carbon content also reduces its ductility and weldability; hence, particular heat treatment should be given to the 4150 alloys. In manufacturing heavy machinery and oil and gas industry, the 4150 steel is, at times, selected for high-stress components owing to its better fatigue resistance and strength.
Applications
4140 steel has been widely used and accepted as versatile and strong. It has unique properties that enable the material to function efficiently under challenging conditions where strength and durability are a must.
Automotive Industry
In the automotive industry, for instance, 4140 steel is often used to manufacture key components such as axles, crankshafts, and gears. Its high strength and wear resistance contribute immensely to the performance and safety of vehicles, making it the best material for parts that are subject to heavy stress while in operation.
Aerospace Manufacturing
The aerospace industry holds 4140 steel in high regard for its ability to meet the most exacting precision and reliability requirements. It finds wide application in the manufacture of aircraft parts, particularly in landing gear and other highly stressed parts. Its high tensile and fatigue strength makes this material admirably suitable for use where failure is not acceptable.
Marine Applications
Due to its corrosion resistance, the 4140 steel is also used in applications at sea. It is a material used in the manufacture of propeller shafts and other parts exposed to seawater thus giving assurance of longevity and dependability at sea applications.
Put Your Custom Parts into Production Today!
Factors to Consider When Processing 4140 Steel
Issues of Machinability
Although 4140 steel provides good machinability when appropriate tools and techniques are applied, the harder materials generally have poorer machinability. The right balance between hardness and machinability has to be determined because poor machining practices will only lead to tool wear and loss of tolerances. Hence, professionals in the field should have a deep understanding of the behavior of the material under various machining processes to ensure satisfactory results.
Welding Practices
In addition to its high carbon and alloy content, WELDING 4140 steel poses many problems, making it much more susceptible to cracking compared to mild steel. Preparation and technique are very important for obtaining strong, reliable welds. An important aspect of the welding process is preheating the steel to prevent cold cracking and to maintain interpass temperatures above 500°F (260°C); otherwise, the possibility of failure is considerably enhanced.
Welders must choose compatible welding consumables to ensure the best results when joining 4140 steel. Modern welding processes, such as Gas Tungsten Arc Welding (GTAW) and Shielded Metal Arc Welding (SMAW), are being used to enhance accuracy and flexibility in welding applications. However, these processes require an experienced operator to control possible complications, such as distortion and hard zones, that can arise during the welding process.
Heat treatment
Heat treatment is an important step in improving the mechanical properties of 4140 steel, such as toughness and fatigue resistance. Proper heat treatment procedures, such as quenching and tempering, are necessary to improve the hardness and overall performance of the material. However, these processes should be done carefully to avoid introducing residual stresses that can lead to cracking. For instance, stress relief by controlled heating to about 1,150°F (621°C) should be carried out to decrease the potential for failure during and after welding.
Fatigue and Wear Resistance
Fatigue and wear resistance are the other aspects that must be considered about 4140 steel. As much as the alloy has considerable abilities in terms of fatigue resistance, it still succumbs to cracking under cyclic loading conditions. This calls for critical design considerations in applications where the steel will undergo repeated stress. Also, resistance to wear is critical when components are exposed to abrasion or friction. The hardness obtained through proper heat treatment significantly enhances this property, hence becoming indispensable in industries relying on high-performance materials.