Cast iron is a multi-functional material used in many industries. The term “cast iron” is the generic name for iron-carbon alloys containing more than 2% carbon. The subclasses of cast iron are numerous, some of them are gray iron and ductile iron. In this article, we will review the differences between ductile iron, gray iron, and cast iron to help engineers select a suitable material for their projects.
Overview of Cast Iron
Cast iron is an alloy of iron and carbon, generally containing more than 2.11% carbon. It also contains trace elements like silicon, manganese, sulfur, and phosphorus, which increase its castability, machinability, wear resistance, and shock absorption properties. The relatively low melting point of cast iron, together with its high fluidity, makes it easy to be poured into molds and produced into complex geometries. As such, cast iron has become a ubiquitous material in many applications.
Types of Cast Iron
Cast irons are classified into several types, mainly based on the structure and morphology of carbon content. The major categories are gray (cast) iron and ductile iron, each having different properties and uses.
Other types of cast iron include:
- Malleable iron: A type of cast iron that is manufactured by exposing white cast iron to annealing heat treatment.
- White cast iron: Features high levels of carbon content and has an eye-catching white, shiny appearance.
- Vermicular graphite iron: graphite is present in a worm-like, stubby form with rounded edges.
What is Gray Iron
Gray iron is distinguished by the presence of flake graphite. This graphite forms a rather special microstructure in which the carbon exists as large, flake-like sheets embedded in the metal matrix. The main elements of gray iron are iron, carbon, silicon, manganese, sulfur, and phosphorus.
Table 1. Composition of gray iron
Iron | C | Si | Mn | P | S |
Remainder | 2.0%~4.0% | 1.0%~2.0% | 0.5%~1.4% | 0.05%~0.50% | 0.02%~0.20% |
Microstructure
The matrix of gray iron typically consists of ferrite, pearlite, or a combination of these. The presence of graphite flakes disrupts the continuity of the metal matrix, therefore making the material less strong in tension. This consequently results in lower tensile strength; however, the material performs extremely well under compressive loads. Stress concentrations occur at the tips of the graphite flakes, which can propagate into cracks and reduce toughness.

Heat treatment cannot change the morphology and distribution of graphite in gray iron, so the use of heat treatment to improve the performance of gray iron is not significant. Heat treatment of gray iron is mainly used to eliminate the internal stress of castings, obtain stable dimensions, improve cutting performance, and increase surface hardness and wear resistance.
Mechanical Properties
Here are some of the key mechanical properties:
Tensile strength. Gray iron has a tensile strength in the range of 100–700 MPa, this is relatively moderate and reflects a rather average resistance to being pulled apart. The strength depends on its matrix composition, with pearlitic matrices offering higher tensile strength compared to ferritic ones.
Yield strength. The yield strength of the gray iron varies between 65.5 and 420 MPa, which gives evidence that it can resist moderate stress before the onset of plastic deformation.
Elongation at the break. Gray iron typically possesses an elongation between 1.0–15.0%. Graphite flakes cause brittleness; thus, very little deformation can be anticipated before failure.
Hardness. The hardness of gray iron lies between 150–300 HB, which provides enough surface hardness for wear resistance in non-impact applications. The hardness depends on the amount of pearlite present in the matrix; the higher the pearlitic content, the higher the hardness.
Table 2. Mechanical properties of gray iron
Materials | Tensile strength | Yield strength | Elongation | Hardness |
Gray iron | 100-700 MPa | 65.5-420 MPa | 1.0-15.0 % | 150-300HB |
Processing Properties
Casting: Excellent casting properties, ideal for complex shapes with good fluidity and a small shrinkage rate.
Machinability: Good, since the presence of graphite acts as a natural lubricant, reducing tool wear and cutting force.
Appearance
Gray iron normally has a dark gray fracture surface with a rough texture. The casting process may also introduce defects such as sand holes and porosity, although these are normally reduced to a minimum in controlled production conditions.
What is Ductile Iron?
Ductile cast iron, also known as nodular cast iron and spheroidal graphite cast iron(S.G. iron), is produced by the addition of a small amount of a nebulizer to molten iron, usually magnesium. The treatment forms spherical shapes of graphite and significantly improves the mechanical properties of the material since there is a reduction in the stress concentration that occurs at the graphite-matrix interface.
Microstructure
The microstructure of ductile iron contains spherical graphite particles that are dispersed evenly in the matrix, which can be ferrite, pearlite, or a mixture of both. The presence of spherical graphite reduces the adverse effect on the matrix, which results in better mechanical properties and an improved balance of performance.
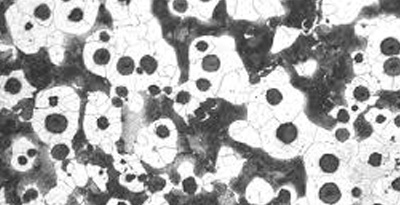
Mechanical Properties
The following are the major mechanical properties of ductile iron:
Tensile strength. Ductile iron has a tensile strength in the range of 400–800 MPa, a measure of its ability to withstand larger pulling forces, the upper end of the range puts it on par with some steels in strength.
Yield strength. Ductile iron has a yield strength of between 250–500 MPa, which is good resistance to permanent deformation under any stress. Combined with its ductility, that makes it more durable under load compared to gray iron.
Elongation. Ductile iron shows an elongation range of 2–18%, which indicates fair to high ductility, compared to other cast irons. The presence of spheroidal graphite nodules in its structure reduces the effect of stress concentrations, which allows the material to deform further before breaking.
Hardness. Its hardness lies between 130–350 HB, depending upon its heat treatment and matrix composition. The higher values of hardness correspond to a higher resistance to wear, whereas lower values are an indication of better machinability.
Table 3. Mechanical properties of ductile iron
Grades | Tensile strength | Yield strength | Elongation | Hardness | Matrix |
QT400-18 | 400 MPa | 250 MPa | 18% | 130-180 HB | ferrite |
QT400-15 | 400 MPa | 250 MPa | 15% | 130-180 HB | ferrite |
QT450-10 | 450 MPa | 310 MPa | 10% | 160-210 HB | ferrite |
QT500-7 | 500 MPa | 320 MPa | 7% | 170-230 HB | ferrite+pearlite |
QT600-3 | 600 MPa | 370 MPa | 3% | 190-270 HB | ferrite+pearlite |
QT700-2 | 700 MPa | 420 MPa | 2% | 225-305 HB | pearlite |
QT800-2 | 800 MPa | 480 MPa | 2% | 245-350 HB | pearlite |
Processing Properties
Casting: Ductile iron has good casting characteristics, however, it is much more difficult to process than gray iron. Both localization and inoculation treatments are required, and this material has a higher shrinkage rate in the solidification process.
Machinability: As with gray iron, ductile iron benefits from the lubricating effect of graphite, but the higher strength increases cutting force and tool wear over gray iron.
Appearance
Ductile iron usually fractures with a silver-gray surface, having a smoother finish compared to gray iron. Due to the high strength and low defect rate, the appearance becomes more refined, which results in a better aesthetic appeal in high-performance applications.
Gray Iron vs. Cast Iron
As an important branch of cast iron, gray iron has the characteristics of flake graphite and is suitable for wear-resistant and shock-absorbing scenarios. Cast iron, as a classification of iron, includes many types, and its performance and application range are significantly different due to different graphite forms.
Table 4. Comparison of gray and cast iron
Features | Gray iron | Cast iron |
Definition | Graphite is distributed in flake form, and the fracture surface is gray. | Iron-carbon alloys usually contain 2% to 4% carbon and include many types. |
Graphite form | Flake | Depending on the type, it can be in the form of flakes, balls, or worms. |
Mechanical properties | High compressive strength and good wear resistance, but low tensile strength and toughness. | The properties of different types of cast iron vary greatly. |
Processability | Good cutting properties | The processing performance varies depending on the graphite morphology and matrix structure. |
Fracture features | The fracture is gray, rough and contains graphite. | The fracture color varies depending on the form of graphite or carbon. |
Price | Lower cost | Costs vary by type |
Ductile Iron vs. Cast Iron
Ductile iron is a member of the cast iron family. It features high strength, toughness, and impact resistance. Cast iron is a broad classification of iron, and its properties and applications vary significantly with the type.
Table 5. Comparison of ductile and cast iron
Features | Ductile iron | Cast iron |
Definition | Graphite is distributed in spherical form, which reduces stress concentration and improves strength and toughness. | Iron-carbon alloys usually contain 2% to 4% carbon and include many types. |
Graphite form | Spherical | Depending on the type, it can be in the form of flakes, balls, or worms. |
Mechanical properties | It has high tensile strength and good toughness, close to or even exceeding that of ordinary steel. | The properties of different types of cast iron vary greatly. |
Processability | Good cutting performance, but slightly higher hardness can easily lead to tool wear | The processing performance varies depending on the graphite morphology and matrix structure. |
Fracture features | The fracture is bright, the surface is smooth, and the graphite is evenly distributed. | The fracture color varies depending on the form of graphite or carbon. |
Price | The cost is higher, but it has excellent performance and long life. | Costs vary by type |
Ductile Iron vs. Gray Iron
Graphite morphology: Gray iron has a flake-shaped graphite that provides a network, which cuts through the metal matrix. Ductile iron contains spherical graphite, which enhances the overall strength of the material by minimizing matrix disruption.
Matrix structure: The matrix of gray iron is very much affected by the presence of graphite flakes, thus reducing its uniformity and mechanical properties. The matrix of ductile iron is less affected by graphite, so it retains its mechanical properties better.
Tensile strength: Gray iron has a tensile strength between 100 to 300 MPa, while ductile iron has a much better tensile strength of 400 to 800 MPa.
Compressive strength: Both materials have good compressive strength; however, ductile iron has a more balanced ratio of compressive to tensile strength of 1.5 to 2.0, whereas gray iron is about 3 to 4.
Plasticity and toughness: Gray iron has low plasticity and toughness. In ductile iron, however, much-enhanced elongation-2% to 18%, and impact toughness are seen.
Casting: Gray iron has good casting characteristics, making it well-suited to complex shapes with low shrinkage. Ductile iron is even more complex in its processing, but it still has good castability, although it tends to shrink more in solidification.
Machining: Both materials have good machinability; however, ductile iron usually requires more force in the machining process due to its higher strength.
Fracture surface: Gray iron has a dark gray, rough fracture surface, while ductile iron fractures in silver-gray with a smoother finish.
Surface quality: Cast iron, on the other hand, has more surface defects, such as sand holes; ductile iron has a much more compact and refined surface finish.
Conclusion
The differences between ductile iron and gray iron lie in microstructure, mechanical properties, and technological features. Compared with gray iron, ductile iron has advantages in strength and toughness due to the spherical graphite, but it has weaker casting and machining properties; on the other hand, gray iron has better casting and machining properties. Gray iron is preferred in applications where complex shapes and good shock absorption are needed, whereas ductile iron is better suited to high-stress applications where strength and toughness must prevail. Understanding these differences is critical in selecting the right material for a specific application, thus guaranteeing maximum performance, long life, and minimum cost.
Put Your Custom Parts into Production Today!
At SogaWorks, we specialize in rapid prototyping and on-demand manufacturing. Supported by the strong network of high-vetted manufacturing plants, we deliver custom CNC machining services with a broad range of materials, including iron, stainless steel, aluminum, and more.