Milling is a subtractive manufacturing process. Climb milling and conventional milling are the two main ways machinists mill parts. Choosing between them is often difficult because both have advantages and disadvantages. In this article, we will learn what they are and the difference between conventional milling and climb milling. We also provide several factors to consider when selecting them to help you make the right decision.
What is Climb Milling?
The types of milling are divided according to the relationship between the rotation direction of the milling cutter and the feed direction of the workpiece. When the rotation direction of the tool is as same as the feed direction of the workpiece, we call it climb milling or down milling. In the climb milling process, the thickness of the workpiece is at its maximum value at the beginning of milling and then gradually decreases until it reaches zero at the end.
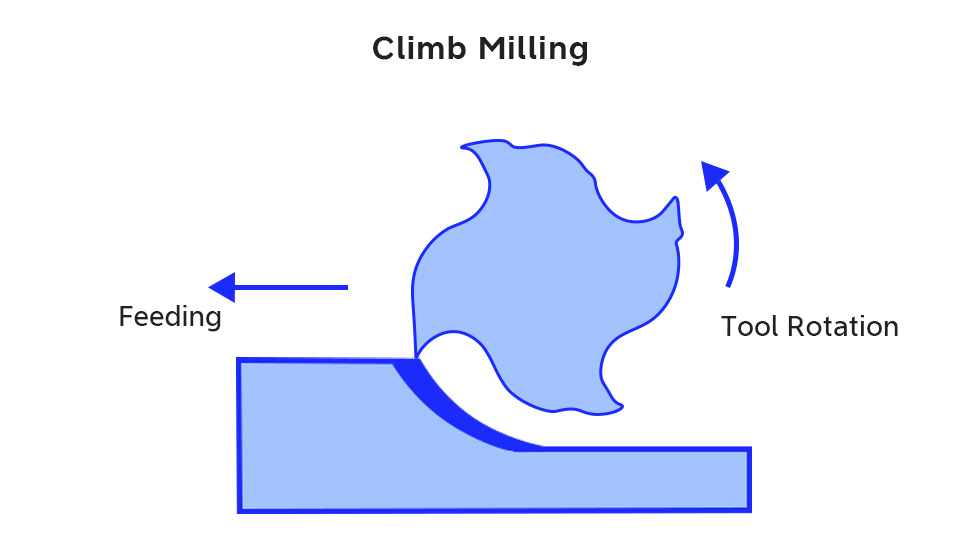
The advantages of climb milling include:
- Longer tool life: When using climb milling, the cutting thickness increases gradually from small to large. This method allows the cutter to cut from shallow to deep, which is beneficial to extend the life of the tool.
- Better surface quality: The cutting force of down milling is small and the damage to the workpiece surface is slight, so a higher precision surface can be machined.
- Low energy consumption: Under the same cutting conditions, power consumption in climb milling is typically 5% to 15% lower than in conventional milling.
What is Conventional Milling?
When the rotation direction of the tool is opposite to the feed direction of the workpiece, it is called conventional milling or up milling. In this process, the thickness of the workpiece is zero at the beginning of milling and then gradually increases until it reaches the maximum at the end.
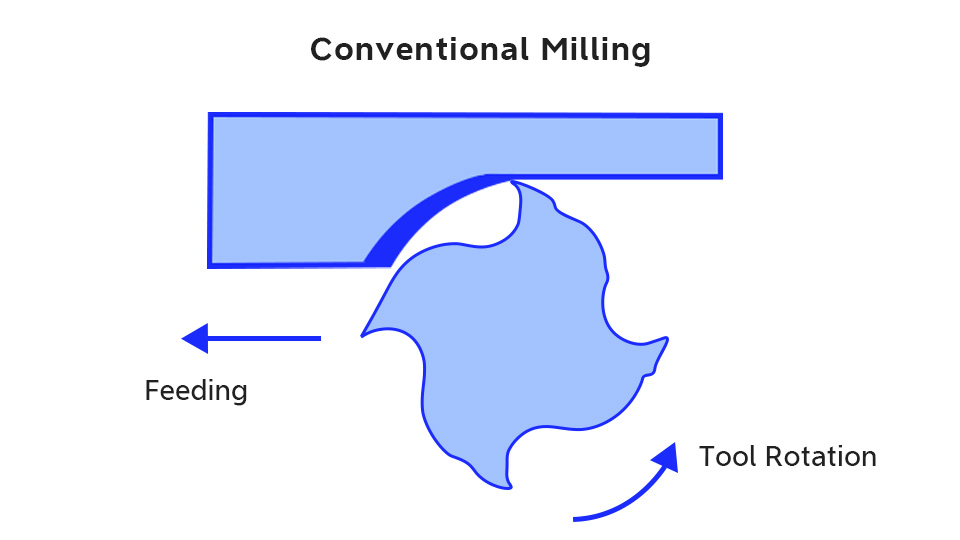
The advantages of climb milling include:
- Protect the tool: The teeth are cut from the machined surface, which will not cause tool breakage.
- Stable workbench: During reverse milling, the cutter teeth cut from bottom to top, there is no slippage when the cutter teeth bite, and the workbench will not move.
Differences Between Climb and Conventional Milling
The table below summarizes the main differences between climb milling and conventional milling.
Feature | Climb milling | Conventional milling |
Cutting Direction | Same as feed direction | Opposite of feed direction |
Thickness | Maximum to zero | Zero to maximum |
Tool wear | Quicker | Slower |
Direction of cutting force | Up | Down |
Vibration | Large | Small |
Energy consumption | Higher | Lower |
Surface roughness | Higher | Lower |
Application | Finish machining | Rough machining |
Thickness Variation
In climb milling, the cutting thickness starts at a maximum value and gradually decreases to zero as the tool contacts the workpiece. This cutting method effectively reduces the initial cutting resistance because the tool can immediately enter the workpiece at the maximum chip thickness, thereby reducing friction and material tearing. In contrast, in conventional milling, the cutting thickness starts at zero and gradually increases to a maximum value. Since the friction generated by the tool when cutting in is large, resulting in greater cutting resistance, this gradual increase in cutting thickness will generate greater friction in the initial stage, which is prone to scratches or irregular cuts on the workpiece surface.
Tool Wear
The tool wear rate in climb milling is relatively slow. This is because, during climb milling, the cutting force acts directly on the workpiece and the machine tool, thereby reducing the friction and temperature accumulation of the tool. In addition, the cutting force in climb milling is more uniform, the tool is less stressed, and the tool life is longer. In conventional milling, since the cutting thickness goes from zero to maximum, the tool has higher friction in the early stage of cutting, which generates more heat, thereby accelerating tool wear. In addition, the increased impact load on the tool, especially when machining hard materials, will further shorten tool life.
Force Direction
In climb milling, the cutting force of the tool is applied downward, which means that the workpiece is pressed against the table of the machine tool, thereby maintaining stability and reducing vibration. This downward cutting force helps to reduce tool deflection while reducing stress loads on the tool and machine tool. In contrast, in conventional milling, the cutting force is upward, which tends to lift the workpiece off the table. Therefore, more clamping force is required to ensure the stability of the workpiece to prevent machining errors or unevenness caused by tool lifting.
Vibration
Vibration is less in climb milling because the cutting force is downward and the workpiece is pressed throughout the process, reducing the gap between the workpiece and the tool, thereby significantly reducing vibration. In conventional milling, the initial friction between the workpiece and the tool is greater due to the upward cutting force, which is prone to greater vibration. This vibration not only affects the surface finish but may also lead to a decrease in machining accuracy, especially when machining harder or irregular surfaces, where the vibration will be more obvious and damage to the tool and equipment will be aggravated.
Energy Consumption
Under the same cutting conditions, climb milling usually consumes 5% to 15% less energy than conventional milling. This is because the cutting force direction of down milling is consistent with the direction of movement of the workpiece, which allows the tool to cut into the material and discharge the chips more easily, reducing cutting resistance and energy consumption. In reverse milling, the direction of movement of the tool is opposite to the direction of movement of the workpiece, which increases the friction and resistance of the tool when entering the workpiece and thus requires more energy to complete the same cutting task.
Surface roughness
Climb milling can produce lower surface roughness because the tool does not produce excessive friction or tearing on the workpiece surface when cutting. The smooth distribution of cutting force in down milling and the control of cutting direction make the workpiece surface smoother and reduce the need for secondary processing. In conventional milling, due to the friction of the tool in the early stage of cutting, surface scratches are easily generated, and as the cutting thickness increases, the workpiece surface will also become more rough or uneven. Vibration during reverse milling will further affect the surface quality.
When to Use Each Milling Process
In milling, climb milling and conventional milling are two common methods. The choice of which method should fully consider the workpiece material and processing requirements:
Material Type
Climb milling is more suitable for processing hard materials because it has lower cutting force, less tool wear, and can obtain a better surface finish. Conventional milling performs better in processing soft materials such as aluminum and brass, and can effectively avoid the adhesion of the tool during climb milling and improve the surface quality.
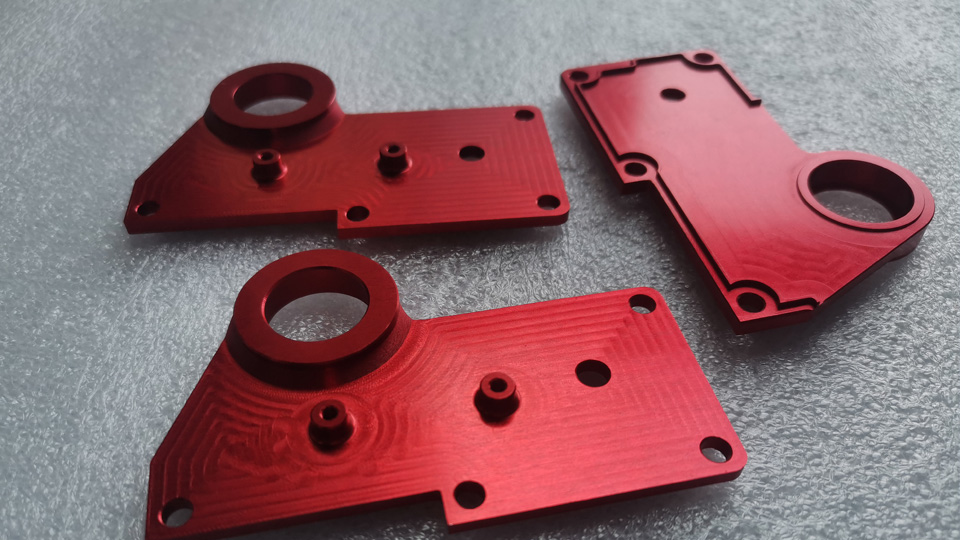
Precision Requirements
Conventional milling is suitable for rough machining because it has higher cutting force and can quickly remove a large amount of material and improve machining efficiency. Climb milling is more suitable for finishing, especially for workpieces with high surface finish requirements, because its cutting process is smoother and can reduce surface roughness.
Surface Condition
When there is a hardened layer or oxide layer on the surface of the workpiece, conventional milling is more suitable because its cutting force direction helps to break the surface hard layer and avoid premature tool wear. For workpieces with rough surfaces, climb milling can provide a better surface finish, but the premise is that there is no hard layer or slag on the surface of the workpiece.
Conclusion
Climb milling and conventional milling have their unique advantages and applications. Climb milling is often used for finishing and applications with high surface quality requirements. In practical manufacturing, the choice of climb milling or conventional milling should based on the different situations. At SogaWorks, we offer comprehensive CNC machining services in China, including CNC milling, turning, and more. Our AI-driven automated platform simplifies the process of sourcing custom parts, making procurement faster, easier, and more efficient!