La fonte d'aluminium offre des avantages tels qu'une grande solidité, une excellente résistance à la corrosion et une grande facilité d'usinage, ce qui en fait un choix privilégié dans des secteurs tels que l'automobile, l'aérospatiale, l'électronique et les biens de consommation. Dans cet article, nous aborderons la composition de l'aluminium moulé, les processus de fabrication, les propriétés, les applications, le contrôle de la qualité et les tendances émergentes.
Qu'est-ce que la fonte d'aluminium ?
Les alliages d'aluminium moulés sont des alliages à base d'aluminium mis en forme par un procédé de moulage. Contrairement à l'aluminium corroyé, qui est façonné par des procédés mécaniques tels que le laminage ou l'extrusion, l'aluminium coulé est fondu et versé dans des moules, puis refroidi et façonné dans la forme souhaitée. Le processus de moulage permet de créer des géométries très complexes qui sont difficiles à produire par d'autres méthodes.
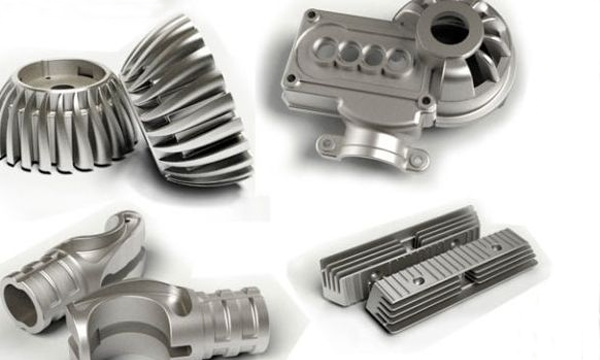
Composition des alliages d'aluminium coulé
Les alliages d'aluminium coulé se composent principalement d'aluminium (Al) et d'un ou plusieurs éléments d'alliage, tels que le silicium (Si), le cuivre (Cu), le magnésium (Mg), le zinc (Zn) et le manganèse (Mn).
Ces éléments sont ajoutés en tant qu'éléments d'alliage pour améliorer des caractéristiques spécifiques.
Éléments | Effets |
Silicium (Si) | Améliore la fluidité, réduit le rétrécissement et améliore la résistance à l'usure. |
Cuivre (Cu) | Augmente la résistance et la dureté mais peut réduire la résistance à la corrosion. |
Magnésium (Mg) | Améliore la solidité et la résistance à la corrosion, en particulier dans les environnements marins. |
Zinc(Zn) | Améliore la coulabilité et la résistance, souvent utilisé dans les alliages à haute résistance. |
Manganèse(Mn) | Améliore la ténacité et la résistance à la fissuration. |
Types d'aluminium moulé
La classification des alliages d'aluminium moulés repose principalement sur la nature élémentaire des principaux éléments d'alliage qui, à leur tour, influencent de manière décisive les propriétés de l'alliage. Il existe quatre catégories principales : A1-Si, Al-Mg, Al-Cu et Al-Zn. Chacune d'entre elles possède ses propres caractéristiques et convient à divers emplois dans plusieurs industries.
Alliages aluminium-silicium (Al-Si)
Les alliages aluminium-silicium sont parmi les alliages d'aluminium moulés les plus utilisés dans la fabrication en raison de leurs extraordinaires propriétés de moulage et de leur bonne résistance à l'usure. Ces alliages contiennent du silicium entre 10% et 25% et ont une faible densité, de faibles coefficients de dilatation thermique et une résistance spécifique élevée. Ces propriétés les rendent appropriés pour des composants tels que les blocs moteurs, les culasses et les roues.
Exemples de grades : A356, A360, A413
Alliages aluminium-magnésium (Al-Mg)
Les alliages Al-Mg restent importants en raison de leur résistance à la corrosion, de leur résistance moyenne à élevée et de leur bonne soudabilité. Avec une teneur en magnésium variant généralement entre 0,5-12%, ces alliages présentent des propriétés mécaniques améliorées. Ils sont utilisés dans les applications aérospatiales à la recherche de matériaux très résistants et légers, comme les structures marines, les trains d'atterrissage des avions et les emballages de produits alimentaires et de boissons.
Alliages aluminium-cuivre (Al-Cu)
Les alliages AI-Cu possèdent une bonne résistance et une excellente usinabilité pour leur teneur en cuivre, généralement comprise entre 2 et 10%. Les principales applications de ces alliages sont l'aérospatiale, l'automobile et l'ingénierie structurelle.
Exemple de grades : A295
Alliages aluminium-zinc (Al-Zn)
Les alliages AI-Zn sont connus pour leur plus grande résistance, en particulier lorsqu'ils sont traités thermiquement. Compte tenu de leurs performances élevées, les alliages Al-Zn sont largement utilisés dans les applications de fabrication aérospatiale.
Exemple de grades : A712.2
Alliages d'aluminium coulés courants
A356 : Matériau pour l'automobile et l'aérospatiale présentant une bonne ductilité et une bonne résistance.
A360 : Bien connu pour sa coulabilité, sa solidité et sa résistance à la corrosion, il est couramment utilisé dans les pièces automobiles telles que les roues et les composants du moteur.
A380 : Réputé pour son étanchéité aux fluides et à la pression, il est largement utilisé pour le moulage sous pression.
A390 : Matériau polyvalent présentant une plus grande solidité, une plus grande dureté et une meilleure résistance à la corrosion.
A413 : Alliage présentant une bonne coulabilité et une remarquable étanchéité à la pression ; une alternative à l'A380.
ADC12 : Alliage largement utilisé en Asie pour le moulage sous pression, avec de bonnes propriétés mécaniques et une bonne coulabilité.
Procédés de la fonte d'aluminium
L'opération de fusion est la première étape de la production d'aluminium moulé. Elle consiste à fondre des matières premières, généralement de l'aluminium primaire, de l'aluminium recyclé et des éléments d'alliage. Le processus de fusion se déroule dans des fours dont la température est comprise entre 700°C et 800°C. Les éléments clés à prendre en compte lors de la fusion sont les suivants :
Prévention de l'oxydation. L'aluminium s'oxyde facilement à l'air libre, formant une couche d'oxyde d'aluminium (Al2O3). Des gaz inertes ou des agents fondants sont utilisés pour réduire l'oxydation.
Homogénéité de l'alliage. L'utilisation d'une méthode appropriée de mélange des éléments d'alliage permet d'obtenir une composition et des propriétés uniformes.
Il existe de nombreuses méthodes de moulage pour la production de pièces en aluminium moulé, toutes avec leurs avantages et leurs inconvénients.
Moulage au sable
Ce procédé de moulage au sable est l'un des plus anciens et des plus polyvalents dans le domaine du moulage de l'aluminium. Il consiste à fabriquer un moule permanent à partir d'un mélange de sable et à y verser du métal en fusion. Cette méthode fonctionne très bien pour les pièces en aluminium plus grandes et plus complexes et permet une certaine flexibilité en ce qui concerne la taille et la forme de la pièce.
Avantages : Faible coût, adapté aux pièces complexes et de grande taille, et options de conception flexibles.
Inconvénients : Par rapport à d'autres méthodes, la précision dimensionnelle et l'état de surface sont moindres.
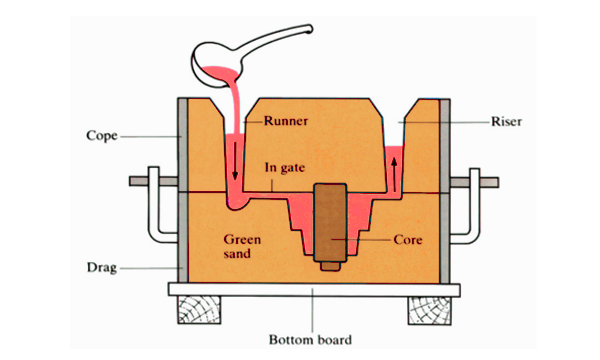
Moulage sous pression
Le moulage sous pression représente la méthode de la rapidité et de l'efficacité. Le procédé consiste à injecter de l'aluminium en fusion directement dans une matrice ou un moule sous très haute pression.
Avantages : Taux de production élevés, excellente précision dimensionnelle et finition de surface lisse.
Inconvénients : Coûts d'outillage initiaux élevés, limités aux petites pièces moulées.
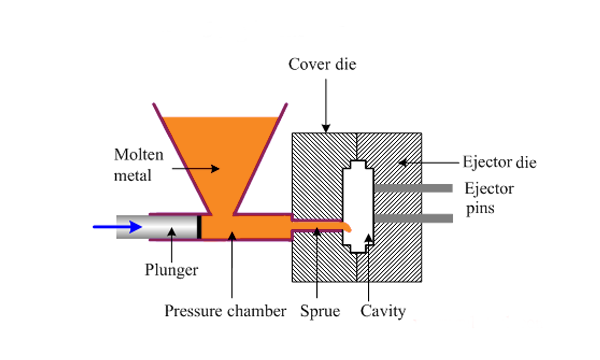
Moulage à la cire perdue
Dans le cas du moulage à la cire perdue, un modèle en cire est enduit d'une boue céramique pour produire un moule, chauffé pour faire fondre la cire, puis rempli d'aluminium en fusion. Cette technique est bien adaptée à la production de pièces moulées en aluminium à paroi mince, avec une épaisseur de paroi minimale de 0,40 mm.
Avantages : Haute précision, excellente finition de surface et possibilité de générer des formes complexes.
Inconvénients : Processus coûteux et chronophage.
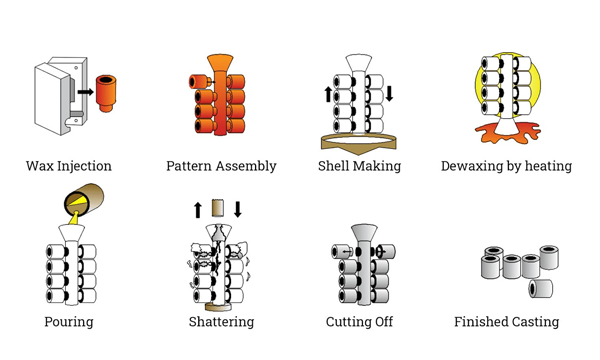
Moulage en moule permanent
La technique du moulage en moule permanent consiste à utiliser des moules métalliques réutilisables. Ce procédé consiste à verser de l'aluminium en fusion dans le moule permanent par gravité ou sous faible pression. Cette méthode est adaptée aux volumes modérés de pièces moulées en aluminium.
Avantages : Bonne finition de la surface, dimensions précises et temps de production plus court que pour le moulage au sable.
Inconvénients : L'outillage est plus coûteux et limité à des géométries simples.
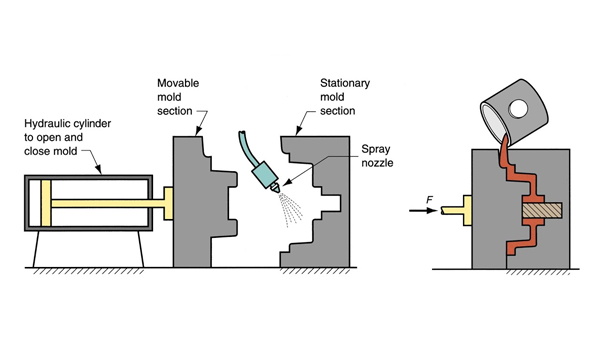
Propriétés et avantages de la fonte d'aluminium
Propriétés mécaniques
Les alliages d'aluminium moulés présentent une gamme de propriétés mécaniques en fonction de leur composition et des traitements thermiques utilisés.
Résistance à la traction | Limite d'élasticité | Élongation | Dureté | Densité |
100-565 MPa | 30-525 MPa | 0.5-28% | 25-170 HB | 2,57-2,95 g/cm³ |
Poids léger
La légèreté est un autre attribut important de la fonte d'aluminium, qui pèse entre 2,57 et 2,95 g/cm³, ce qui la rend plus légère que d'autres matériaux tels que l'aluminium. fonte et de l'acier. Ce poids plus faible lui confère un rapport résistance/poids élevé, ce qui est avantageux lorsque l'on recherche à la fois la résistance et la légèreté.
Résistance à la corrosion
Les alliages d'aluminium coulé sont recouverts en surface d'une couche d'oxyde qui forme un bouclier protecteur, ce qui leur confère une excellente résistance à la corrosion. C'est pourquoi ils sont utilisés dans des applications en environnements corrosifs et hostiles, comme les composants marins et automobiles.
Conductivité thermique et électrique élevée
La fonte d'aluminium est utilisée de manière appropriée pour les échangeurs de chaleur, les boîtiers électroniques et les composants électriques, car l'aluminium se caractérise également par une conductivité thermique et électrique élevée.
Conductivité thermique : 87-233 W/m-K
Conductivité électrique : 21-45 %
Haute qualité
Les alliages d'aluminium moulés offrent une bonne précision dimensionnelle et une bonne finition de surface. La tolérance dimensionnelle est normalement comprise entre IT6 et IT7, et dans certains cas, elle peut atteindre IT4. La rugosité de la surface est généralement comprise entre Ra 5 et Ra 8, ce qui réduit la nécessité d'un traitement ultérieur. Il convient également de noter que les alliages d'aluminium moulés offrent une résistance et une dureté plus élevées que les pièces moulées en sable, la résistance étant normalement améliorée de plus de 25% à 30%, tandis que l'allongement est réduit d'environ 70%. Les propriétés mécaniques, bien qu'il y ait une baisse de l'allongement, conviennent encore à de nombreuses applications. En outre, la fonderie d'aluminium peut mouler des pièces complexes à parois minces, telles que des pièces moulées en alliage de zinc ayant une épaisseur de paroi minimale de 0,3 mm et des pièces moulées en aluminium ayant une épaisseur minimale de 0,5 mm ; la production comporte des trous de coulée d'un diamètre aussi petit que 0,7 mm, et les filets ont un pas minimal de 0,75 mm seulement.
Avantages économiques
En raison de la grande précision et de la finition de la surface des pièces en aluminium moulé, elles ne nécessitent généralement pas ou peu d'opérations d'usinage supplémentaires. Cette amélioration concerne l'utilisation des métaux, la réduction des équipements d'usinage importants et les économies de main-d'œuvre. En outre, les pièces en aluminium moulé sont relativement moins chères en raison de l'efficacité du processus de moulage.
Contrôle de la qualité dans la fabrication de l'aluminium moulé
Détection des défauts
La porosité, le retrait, les fissures et les inclusions sont quelques-uns des défauts qui peuvent survenir lors de la coulée de l'aluminium. Différentes méthodes sont utilisées pour détecter les défauts :
- Inspection visuelle : Observation des défauts de surface.
- Radiographie et tomodensitométrie : Détection des défauts internes.
- Contrôle par ultrasons : Mesure de la solidité interne et de l'épaisseur.
- Inspection par ressuage : Ceux qui révèlent les fissures superficielles.
Précision dimensionnelle
La précision du moulage est très importante, essentiellement pour le bon fonctionnement et l'ajustement. Diverses techniques telles que les machines à mesurer les coordonnées (CMM) et les systèmes de balayage laser sont utilisées pour garantir la précision des dimensions.
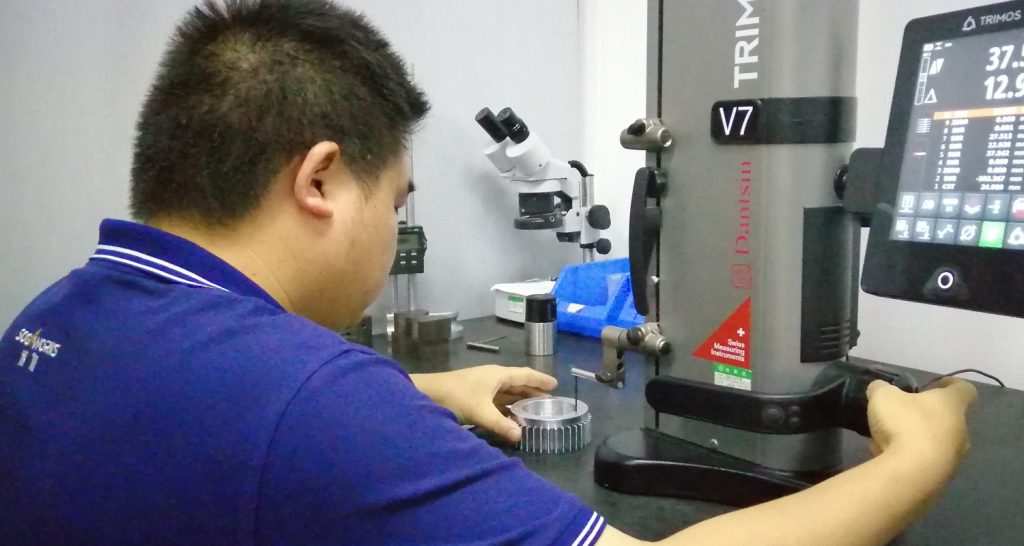
Finition de la surface
La finition de la surface est obtenue par anodisation, polissage et revêtement. Anodisation est un traitement de surface couramment utilisé qui augmente la résistance à la corrosion et améliore l'apparence.
Tendances futures dans la fabrication de l'aluminium moulé
Fabrication additive
Impression 3D de métaux gagne rapidement en popularité, offrant un moyen efficace et rapide de construire des géométries complexes tout en gaspillant peu de matériau. Elle est particulièrement adaptée au prototypage et aux petites séries.
Fabrication durable
Le métal a une durée de vie beaucoup plus longue et le processus de recyclage de l'aluminium ne nécessite qu'environ 5% d'énergie, ce qui le rend plus respectueux de l'environnement. Les industries se concentrent avec succès sur les systèmes de recyclage en boucle fermée pour minimiser les déchets.
Alliages avancés
Des recherches sont toujours en cours pour synthétiser de nouveaux alliages d'aluminium moulé possédant des propriétés supérieures telles qu'une plus grande résistance à la traction, une meilleure conductivité thermique et une meilleure résistance à la corrosion.
Conclusion
La fonte d'aluminium est l'un des matériaux les plus importants dans la fabrication moderne, car elle offre un mélange de légèreté, de résistance et de polyvalence recherché par de nombreuses industries. Comprendre la composition, le processus de fabrication, les propriétés et les applications de la fonte d'aluminium permet aux fabricants d'utiliser ce matériau d'une manière qui se prête à la création de produits innovants et performants. Au fur et à mesure que l'industrie évolue, les progrès en matière de légèreté, fabrication additiveet la durabilité élargiront encore les horizons de la fonte d'aluminium. Ce guide est une mine d'informations pour tous ceux qui souhaitent approfondir leur connaissance de la fonte d'aluminium et de sa position dans l'environnement de fabrication.